- Joined
- Mar 7, 2007
- Messages
- 729
- Reaction score
- 2,341
Made a decision to duplicate a patchbox I did on another rifle in 2012 and gave away. I don't have one like it and I like the asymmetric design. Here is the layout.....
The door in 0.050" material. The side pieces are cut out of .032" brass.....
Then I contoured the door to the curvature of the stock and prepared one side of the hinge I made earlier for silver soldering to the door.....
I ran out of the appropriate thickness of brass sheet to make the top of the box. Material is on order. Once that is cut out and contoured, I will attach the opposite side of the hinge in the same way.
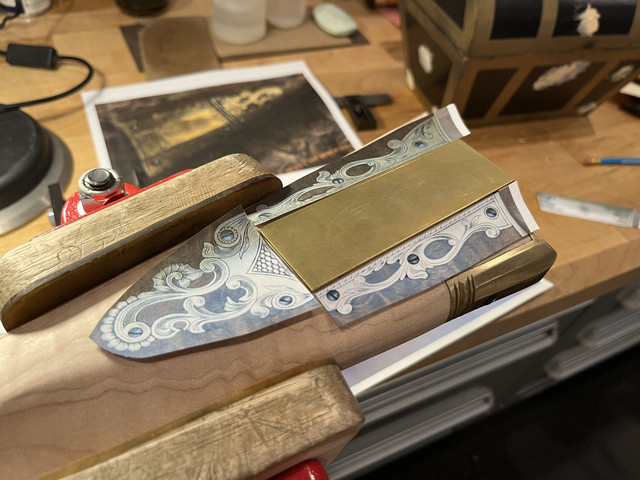
The door in 0.050" material. The side pieces are cut out of .032" brass.....
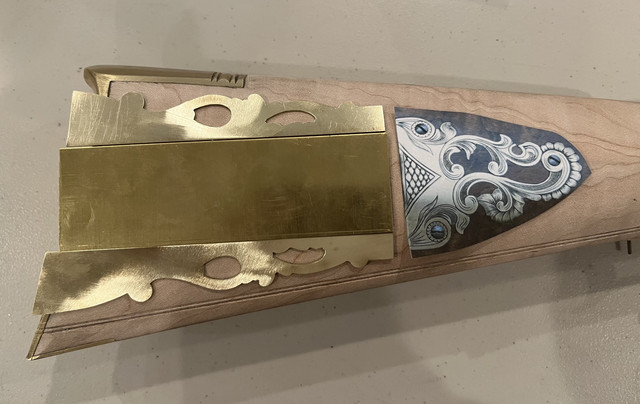
Then I contoured the door to the curvature of the stock and prepared one side of the hinge I made earlier for silver soldering to the door.....
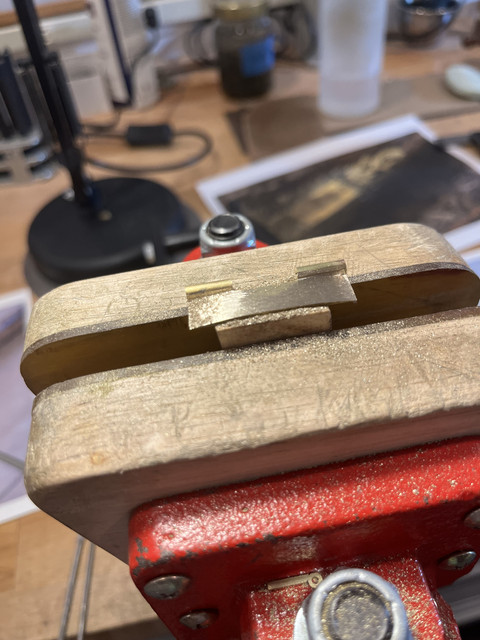
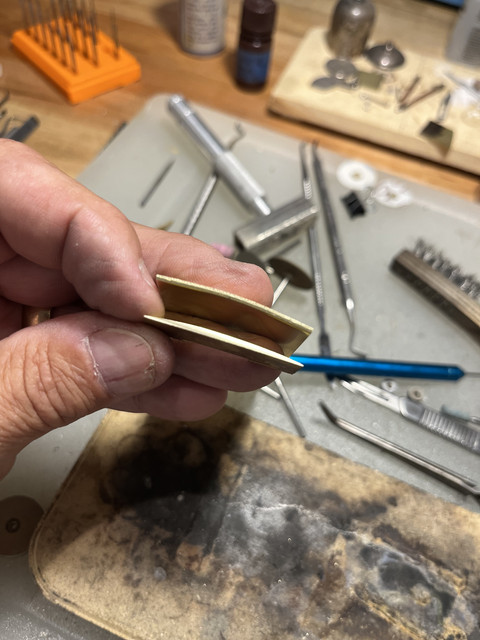
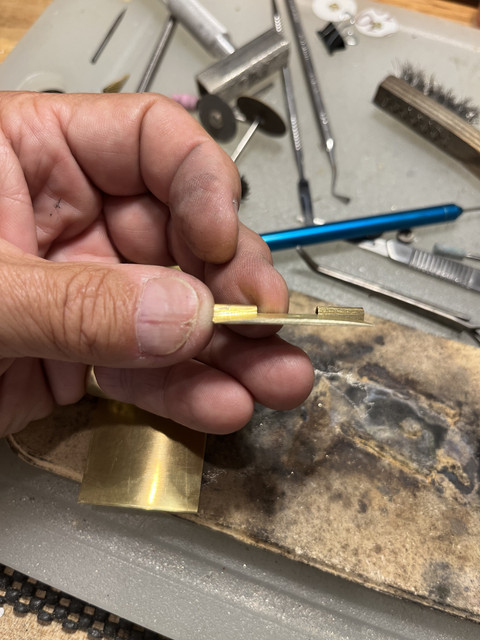
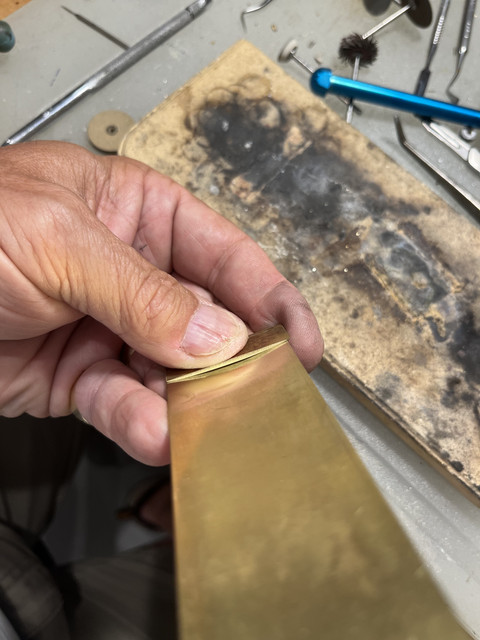
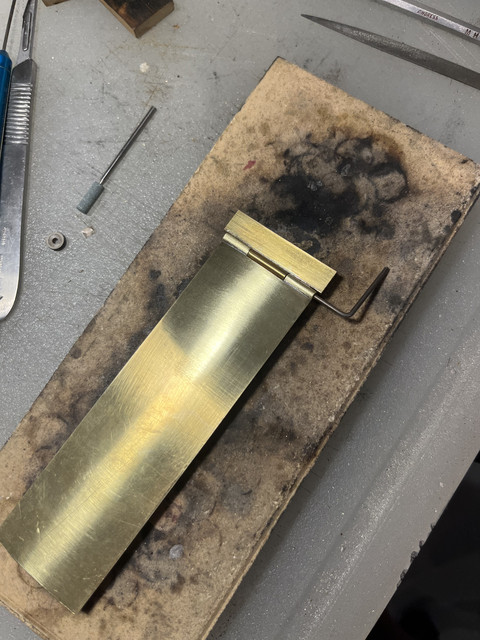
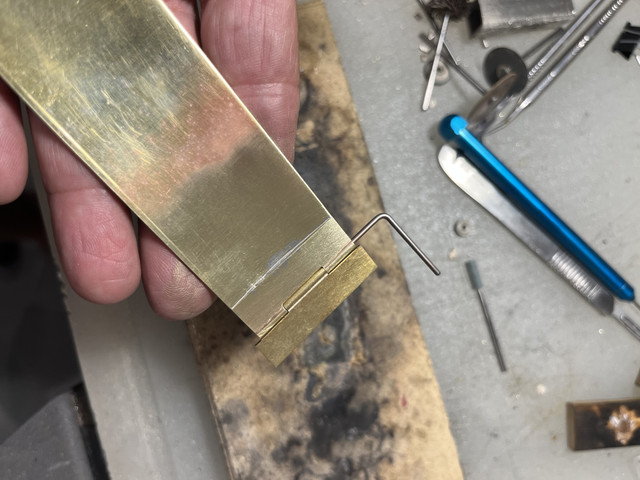
I ran out of the appropriate thickness of brass sheet to make the top of the box. Material is on order. Once that is cut out and contoured, I will attach the opposite side of the hinge in the same way.