The recent discussion of a possible 1700's pipe hawk reference in Minnesota got me thinking about those sheet iron pipes again.
I did a little ... tinkering ... yesterday and today. I'm supposed to be resting my back a bit, but I just couldn't set here and do nothing. Although, the few minutes I did spend out in the shop preparing the metal for this bit of "tinkering" let me know I was pushing things. Plus temps back in the mid 80's with similar humidity didn't help much.
I played around with my sheet iron pipe pattern, size, and final shaping. I kind of like the longer stem, and also the gentle curve. The surviving originals were straight stemmed, but there's just something about that curved stem that catches the ... imagination.
And I made a few of the regular size/shape sheet iron pipes as well.
Yes, an ... interesting ... way to spend a little recovery time.
Mikey - yee ol' grumpy German blacksmith out in the Hinterlands
I did a little ... tinkering ... yesterday and today. I'm supposed to be resting my back a bit, but I just couldn't set here and do nothing. Although, the few minutes I did spend out in the shop preparing the metal for this bit of "tinkering" let me know I was pushing things. Plus temps back in the mid 80's with similar humidity didn't help much.
I played around with my sheet iron pipe pattern, size, and final shaping. I kind of like the longer stem, and also the gentle curve. The surviving originals were straight stemmed, but there's just something about that curved stem that catches the ... imagination.
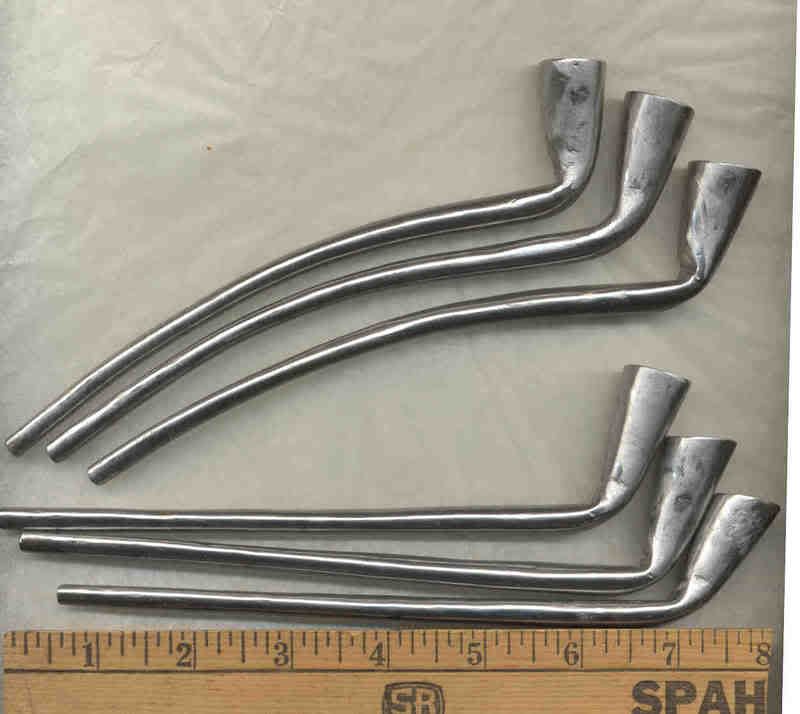
And I made a few of the regular size/shape sheet iron pipes as well.
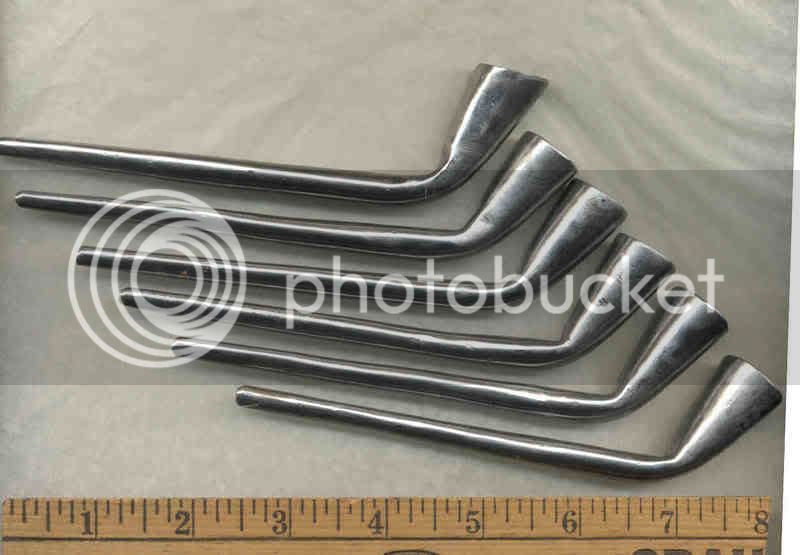
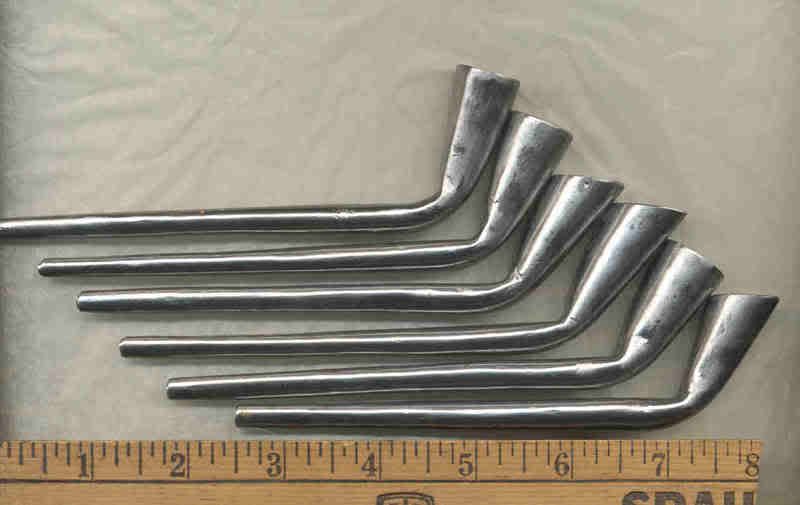
Yes, an ... interesting ... way to spend a little recovery time.
Mikey - yee ol' grumpy German blacksmith out in the Hinterlands