- Joined
- Aug 25, 2003
- Messages
- 6,535
- Reaction score
- 1,512
My first attempt at a sword scabbard. A bit of a challenge, but after three trys on the leather, it all worked out. All steel fittings. The tip is three pieces silver brazed together. Two halves and a bottom plug. The throat is also three pieces. The main body with a brazed seam in back, and 650° silver soldered top plate. The frog hook was made from a bar of 3/8" steel, sawed and filed to shape, then pinned and brazed to the throat. The sword was made by Jared Secrest under the guidance of Kyle Willyard, light in weight, and wonderfully balanced.
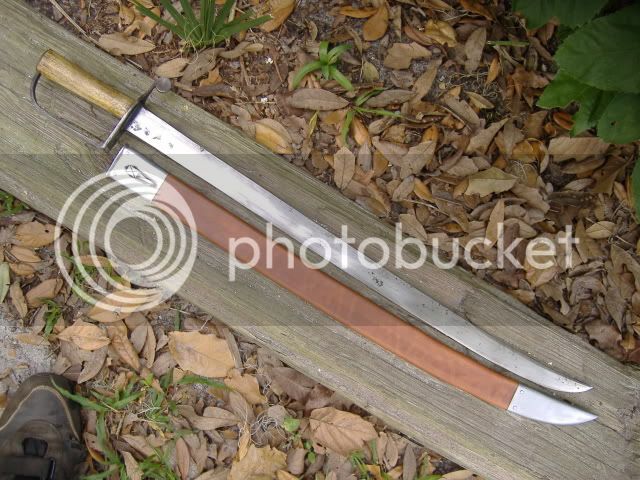
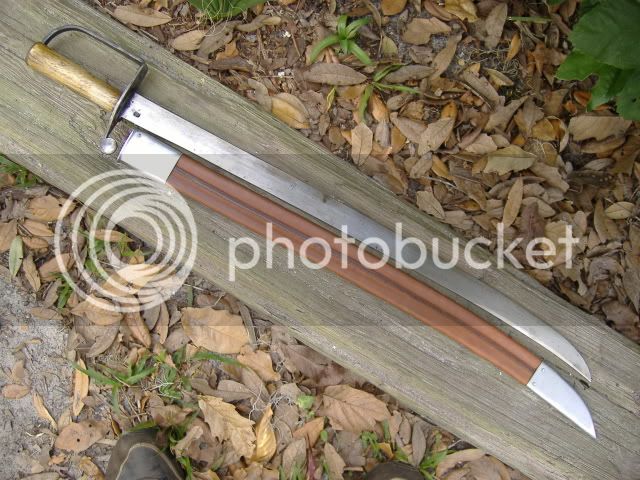
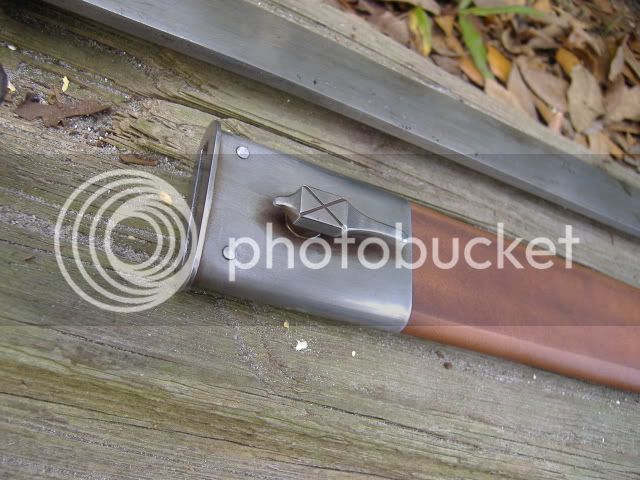
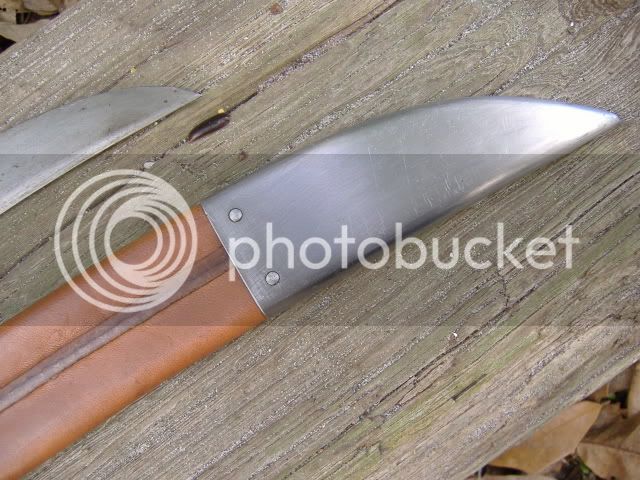