fischereco2
36 Cal.
- Joined
- Aug 7, 2014
- Messages
- 95
- Reaction score
- 1
Here's a little pocket knife I just finished. It's not based on anything in particular other than those el-cheapo Pakistani ones you see floating around. This was more of a proof of concept piece since I've never made any kind of slip-joint folder before. Definitely way more painstaking than I anticipated and there a lot of things wrong with this knife, but lessons learned.
In the future I think I'll try brazing the bolsters on instead of using pins. I wasn't super careful when drilling all of the holes so my scales were slightly mismatched. This meant I had to force them together, which caused one of my bone panels to blow out in the process. I also have this problem every once and awhile where my blades develop these shallow spots along the edge, making the whole thing kind of wavy. I do my best to make sure everything is even before I start the sharpening process, so I'm not sure why this always seems to happen in the same spot. It basically ends up looking like a used knife that's been over-sharpened. Also I forgot to forge in the nail-nick, but luckily the tension is just right so it doesn't need one.
I have a goal for this year, which is to perfect a few basic styles of knife and make enough of each of them to sell on a trade blanket at one of the big fort events around here next year. I think with a little more practice and fine tuning I'll get there.
Anyway, thanks for looking.
In the future I think I'll try brazing the bolsters on instead of using pins. I wasn't super careful when drilling all of the holes so my scales were slightly mismatched. This meant I had to force them together, which caused one of my bone panels to blow out in the process. I also have this problem every once and awhile where my blades develop these shallow spots along the edge, making the whole thing kind of wavy. I do my best to make sure everything is even before I start the sharpening process, so I'm not sure why this always seems to happen in the same spot. It basically ends up looking like a used knife that's been over-sharpened. Also I forgot to forge in the nail-nick, but luckily the tension is just right so it doesn't need one.
I have a goal for this year, which is to perfect a few basic styles of knife and make enough of each of them to sell on a trade blanket at one of the big fort events around here next year. I think with a little more practice and fine tuning I'll get there.
Anyway, thanks for looking.
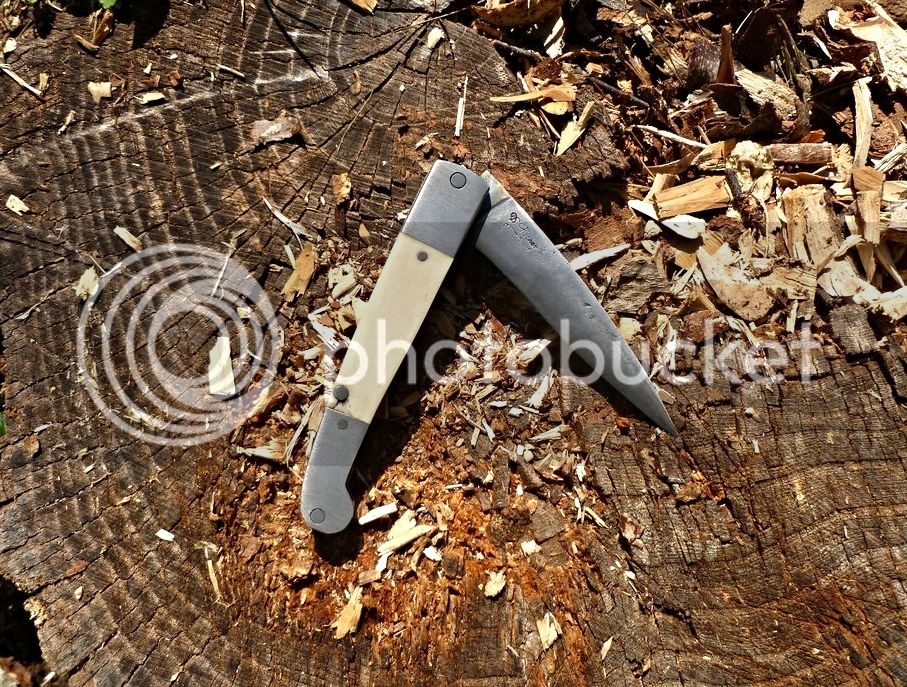
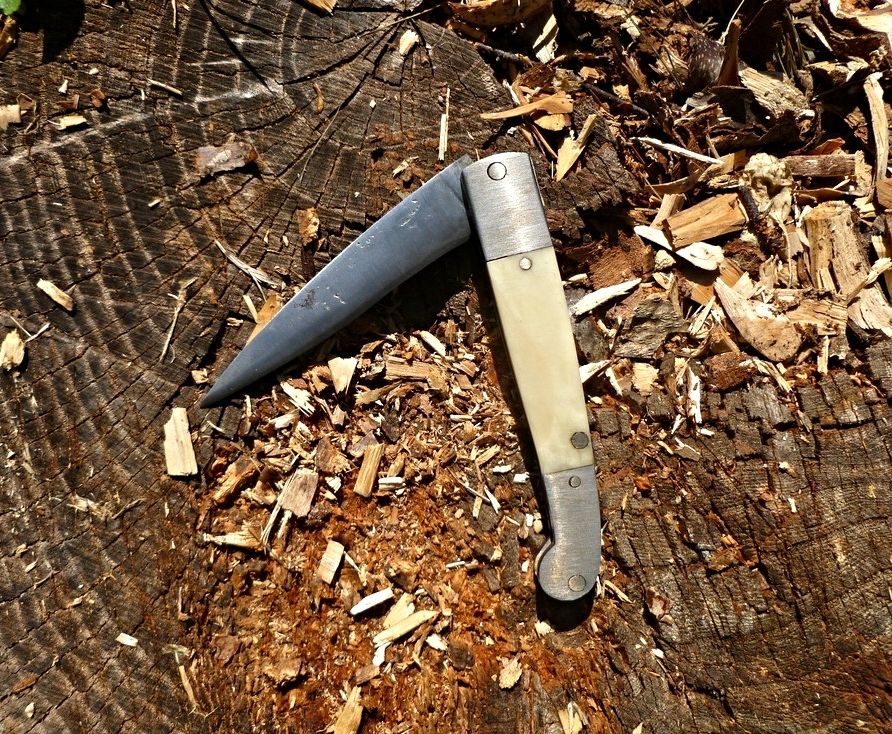
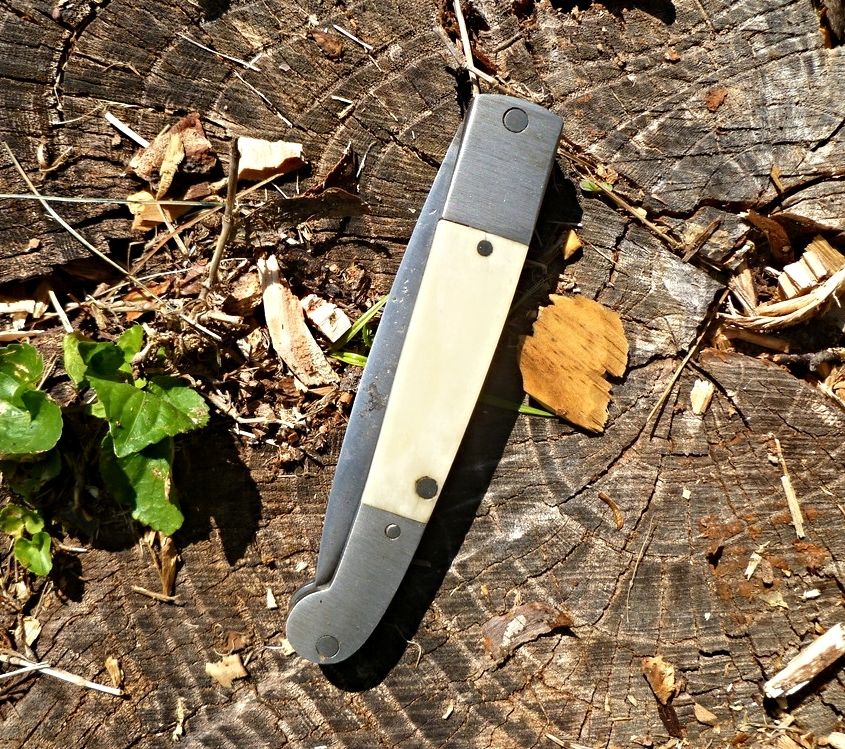