I been working on this project for sometime now.
Taking original JP Beck hardware and having it digitally scanned to .001mm I then had it 3D printed to .01mm tolerances in plastic.
Those 3D models were scaled to account for brass shrinkage and clean up.
I made the cope and drag from some oak.
I plan to use finer sand than 130 mesh next time and pack it a little tighter.
See the YouTube video below I made showing my progress/process:
Please share any advice, or tips. Hopefully I will try some butt plates next.
Want my Next build to be all me except for the lock and barrel. Through maybe one day those two ?🤣
Taking original JP Beck hardware and having it digitally scanned to .001mm I then had it 3D printed to .01mm tolerances in plastic.
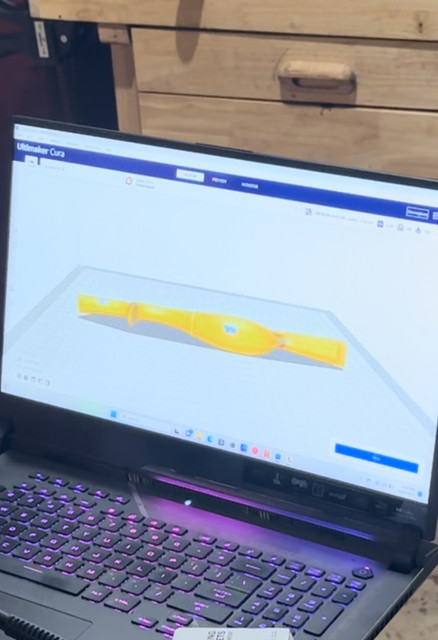
Those 3D models were scaled to account for brass shrinkage and clean up.
I made the cope and drag from some oak.
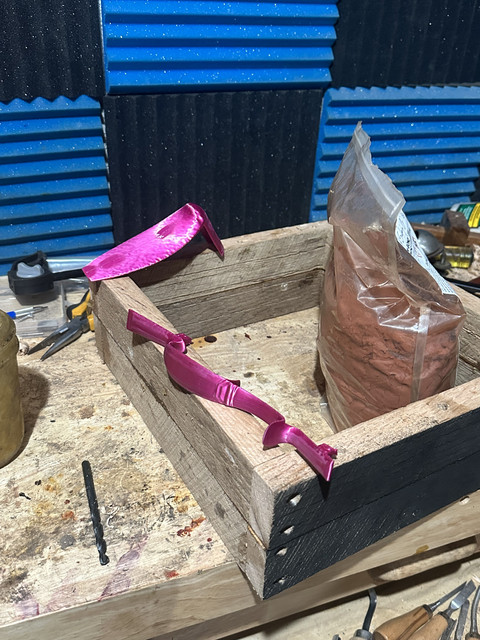
I plan to use finer sand than 130 mesh next time and pack it a little tighter.
See the YouTube video below I made showing my progress/process:
Please share any advice, or tips. Hopefully I will try some butt plates next.
Want my Next build to be all me except for the lock and barrel. Through maybe one day those two ?🤣

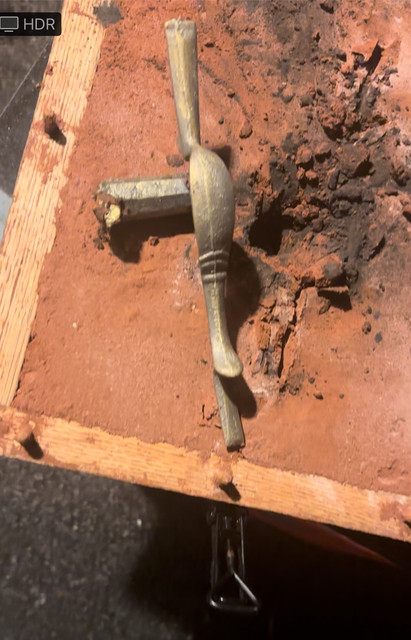