Erzulis boat,
Here you go. :thumbsup:
I am sure that I will leave out some steps, so feel free to ask any questions. :v
Ketland lock from TRS
I always start out with the lock plate. First thing I make sure that its flat and then I start in with a single cut file, and finish with a bit of sandpaper glued to a flat piece of hardwood. I try to keep everything flat and square to keep from digging holes. Mind some casting flaws can never be fully removed.
Next step is where the lathe comes in handy to clean up the tumbler and to drill the hole for the tumbler/**** screw. The tumbler hole in the lock plate is the only one that I will drill using the casting mark from the face side laying the plate on a flat surface.
The bridal is next first making sure that the guide pin is drilled in the right location so the bridle, sear, and tumbler will be aligned properly.
Here you go. :thumbsup:
I am sure that I will leave out some steps, so feel free to ask any questions. :v
Ketland lock from TRS
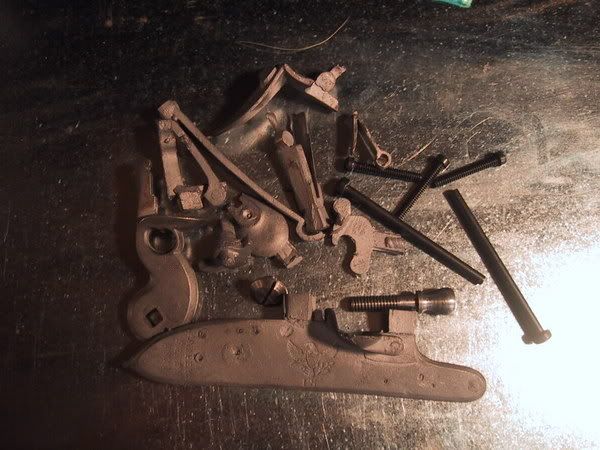
I always start out with the lock plate. First thing I make sure that its flat and then I start in with a single cut file, and finish with a bit of sandpaper glued to a flat piece of hardwood. I try to keep everything flat and square to keep from digging holes. Mind some casting flaws can never be fully removed.

Next step is where the lathe comes in handy to clean up the tumbler and to drill the hole for the tumbler/**** screw. The tumbler hole in the lock plate is the only one that I will drill using the casting mark from the face side laying the plate on a flat surface.
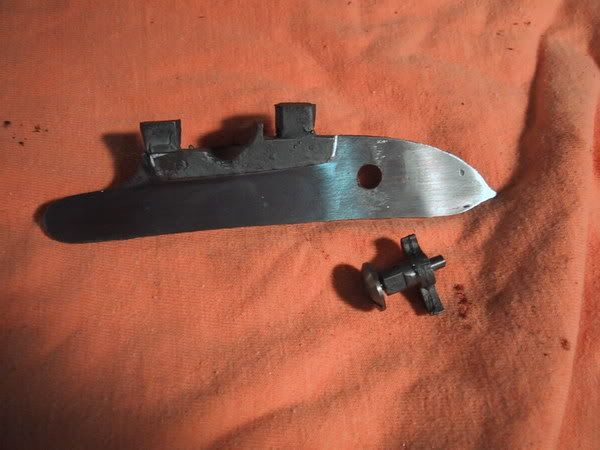
The bridal is next first making sure that the guide pin is drilled in the right location so the bridle, sear, and tumbler will be aligned properly.
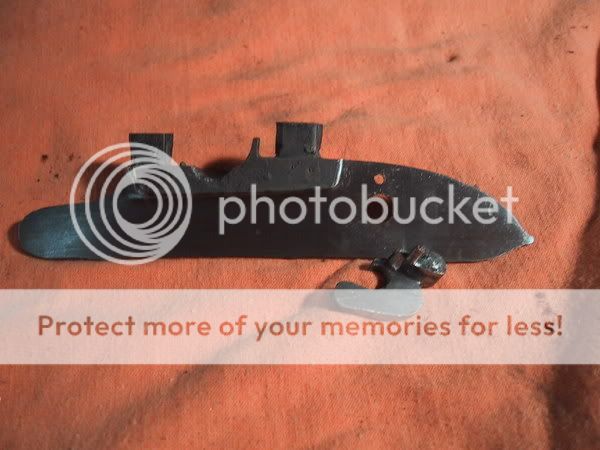