Not to throw the thread off subject, but here's a few pics of my soon to be pistol TG that I'm making out of sheet brass.
In the bottom two pics you can see the broken cast brass (not really brass....some kind of junk metal. It snapped like a string bean at the narrow point and had casting voids of 50% in that spot!).
Well, I can at least use it for a model to follow. The upper left pic shows where I wrapped the cut out shape of brass(annealed of course) around the hardwood "anvil" that I shaped from leftover maple. The upper right shows some rough cleanup of that piece.
The two lower pics show the "lollipop"which I will (using brass color silver solder) solder onto the main piece so it will look like the broken piece. Once I solder that lollipop on I'll bend it to be the front extension of the TG. Then once bent I'll solder on a tab to pin in the pistol.
The rear tail I have yet to make, but once I do that I'll brass solder it to the rear of the main piece.
Once all that's done I'll file\sand\polish it to my finish shape.
I know it's somewhat easier to buy a TG. But my recent experiences with cast brass have not been good. So, I'll just take the time to make one. Besides, then I can "brag" to my shooting buddies that I did it.
In the bottom two pics you can see the broken cast brass (not really brass....some kind of junk metal. It snapped like a string bean at the narrow point and had casting voids of 50% in that spot!).
Well, I can at least use it for a model to follow. The upper left pic shows where I wrapped the cut out shape of brass(annealed of course) around the hardwood "anvil" that I shaped from leftover maple. The upper right shows some rough cleanup of that piece.
The two lower pics show the "lollipop"which I will (using brass color silver solder) solder onto the main piece so it will look like the broken piece. Once I solder that lollipop on I'll bend it to be the front extension of the TG. Then once bent I'll solder on a tab to pin in the pistol.
The rear tail I have yet to make, but once I do that I'll brass solder it to the rear of the main piece.
Once all that's done I'll file\sand\polish it to my finish shape.
I know it's somewhat easier to buy a TG. But my recent experiences with cast brass have not been good. So, I'll just take the time to make one. Besides, then I can "brag" to my shooting buddies that I did it.


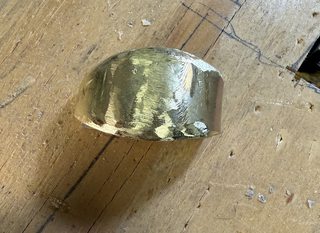
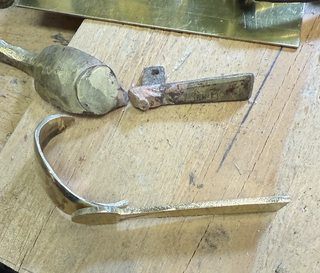
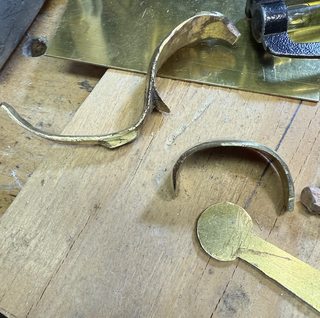