Lot's of people ask how I jug choke a barrel. I won't try to do a how-to "tutorial" here because lots of the actual work is by "feel". One can feel how the tool is cutting and by experience learn to recognize the right feeling and what to do if it is not right. But anyhow, this is what I use to cut jug chokes. The tool is guided by the bore itself and thus is always straight and centered to the bore. Don't even try to cut a chrome plated bore.
This is the tool in working position in the bore.
This is the tool just removed and heavily loaded with cuttings from a "roughing cut".
This shows the tool disassembled for cleaning, note the coarse cuttings.
This shows the tool completely disassembled with micrometer and telescoping gage for measuring the depth of the recess.
This shows the fine powder cuttings typical of a light finishing cut.
The tool shown is for 16 and 20 gauge guns. The wooden backer is reinforced with AccraGlass bedding compound. I use the same cutter with a different backing for 10, 12 and 14 gauge and for that I milled the backer out of Derlin plastic. It is important that the cutter fit very tightly into the slot in the backing, any "wiggle room" will lead to chattering.
Keep the cutting edge sharp, use lots of cutting oil, take it slowly, remove and clean the cutter very frequently, go easy on the finish cuts and it's a snap.
This is the tool in working position in the bore.
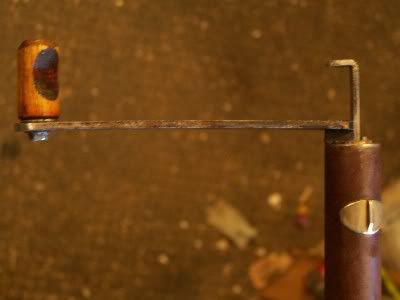
This is the tool just removed and heavily loaded with cuttings from a "roughing cut".
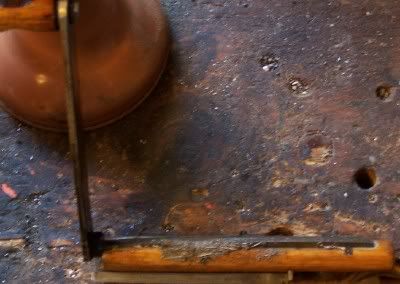
This shows the tool disassembled for cleaning, note the coarse cuttings.
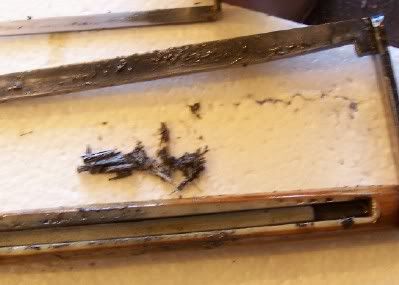
This shows the tool completely disassembled with micrometer and telescoping gage for measuring the depth of the recess.
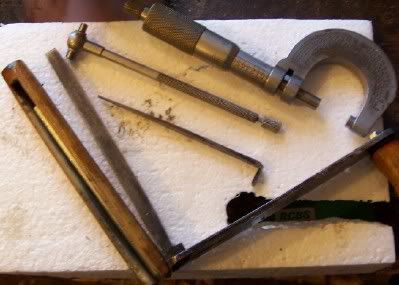
This shows the fine powder cuttings typical of a light finishing cut.
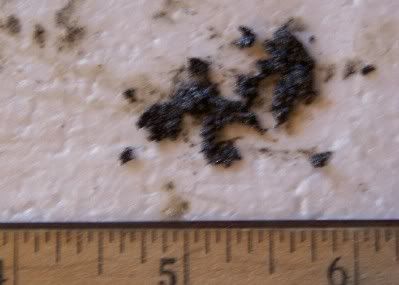
The tool shown is for 16 and 20 gauge guns. The wooden backer is reinforced with AccraGlass bedding compound. I use the same cutter with a different backing for 10, 12 and 14 gauge and for that I milled the backer out of Derlin plastic. It is important that the cutter fit very tightly into the slot in the backing, any "wiggle room" will lead to chattering.
Keep the cutting edge sharp, use lots of cutting oil, take it slowly, remove and clean the cutter very frequently, go easy on the finish cuts and it's a snap.