- Joined
- Mar 7, 2007
- Messages
- 710
- Reaction score
- 2,221
Here are the first two parts for the spring arrangement to advance the reamer while I turn the handle, the spring and the movable spring stop. The spring rate is ~104 pounds per inch of compression, so it should be more than enough to force the reamer into the cut without me having to push. I'm sure I was not applying more than 40 or 50 pounds of force when I was struggling to cut a few inches. The rest of the arrangement is a clap trap of all-thread rods and lumber. I didn't want to spend too much time and effort making a sophisticated rig....I don't think I will be doing this type of work more than once in a lifetime. 
I'll take more pictures when I have it all put together and fins out if it works. ??
I'll take more pictures when I have it all put together and fins out if it works. ??
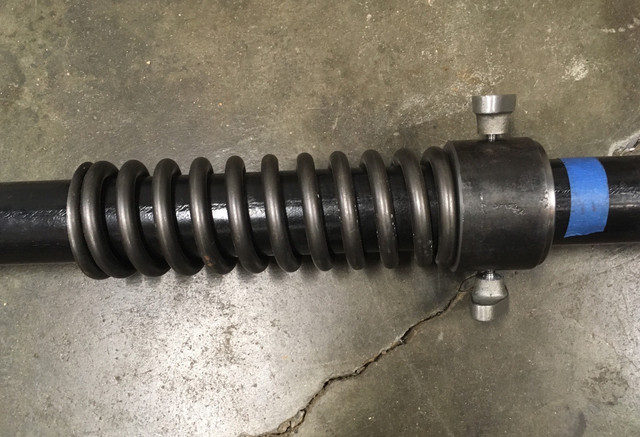