Good advice. I'll try the bag balm. Usta use that stuff a lot when I worked on cars for a living. Good stuff. :thumbsup:
Glad to hear some of you guys are enjoying this topic.
OK, some words about pocket and strap placement;
Sometimes, if I use a larger pocket and/or a smaller back panel, the strap and pocket stitching may interfere with one another. Think about this ahead of time to avoid any issues when sewing them on.
I have done several bags where the inside seam of the strap winds up inside of the pocket. When this happens I just work around it by sewing the inside strap seams, then the pocket, then the outside strap seams. You don't want to have to try and sew inside of a pocket if you can help it.
On this particular bag there won't be any such issues. The strap is located clear of the pocket. Notice here that the strap stitching holes are placed at an 11 degree angle relative to the top of the bag. This makes the bag ride better across your shoulder.
We will stitch the pocket on now. Actually we could have done this first but I wanted to show you some of the more interesting stuff. Pockets are relatively straight forward and boring...
The top edges of the pocket seams are a stress point so I like to backstitch the ends on both sides for extra strength. Just start about 5 holes below one end and then stitch up to the top.
Then, reverse direction and stitch all the way around to the other end. Backstitch 4 or 5 stitches here to lock everything in.
Since the strap is not going to give me any problems on this bag, I'm going to hold off on it for a while yet. It's easier to sew when you don't have to deal with a strap flapping around all over the place.
Now I'll start on the front panel. For this step you will need a strip of welting that is a couple of inches longer than the entire seam around the front panel. Don't cut it short.
The strip of welting should be placed shiny side toward the shiny side of the front panel and the front panel placed shiny side against the shiny side of the back panel. Here again, start at the center of the front panel and the center of the gusset and stitch toward one end of the gusset just like we did earlier.
When you get to the end of the gusset, stop and backstitch 4 or 5 stitches to lock it in just like we did on the back panel. Do NOT trim the welt this time.
Then stitch the other side the same way starting in the same hole. Backstitch again at this end of the gusset too. Now this thing is really starting to look like a bag!
Next installment coming soon.
Glad to hear some of you guys are enjoying this topic.
OK, some words about pocket and strap placement;
Sometimes, if I use a larger pocket and/or a smaller back panel, the strap and pocket stitching may interfere with one another. Think about this ahead of time to avoid any issues when sewing them on.
I have done several bags where the inside seam of the strap winds up inside of the pocket. When this happens I just work around it by sewing the inside strap seams, then the pocket, then the outside strap seams. You don't want to have to try and sew inside of a pocket if you can help it.
On this particular bag there won't be any such issues. The strap is located clear of the pocket. Notice here that the strap stitching holes are placed at an 11 degree angle relative to the top of the bag. This makes the bag ride better across your shoulder.
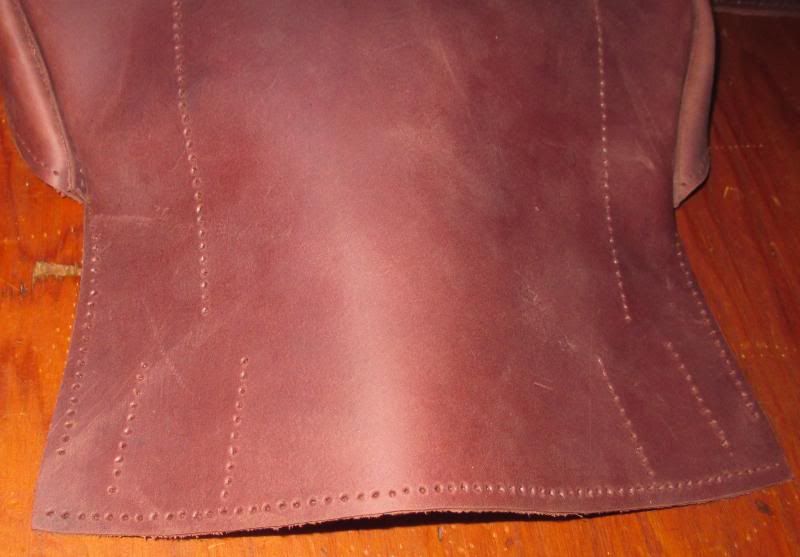
We will stitch the pocket on now. Actually we could have done this first but I wanted to show you some of the more interesting stuff. Pockets are relatively straight forward and boring...
The top edges of the pocket seams are a stress point so I like to backstitch the ends on both sides for extra strength. Just start about 5 holes below one end and then stitch up to the top.
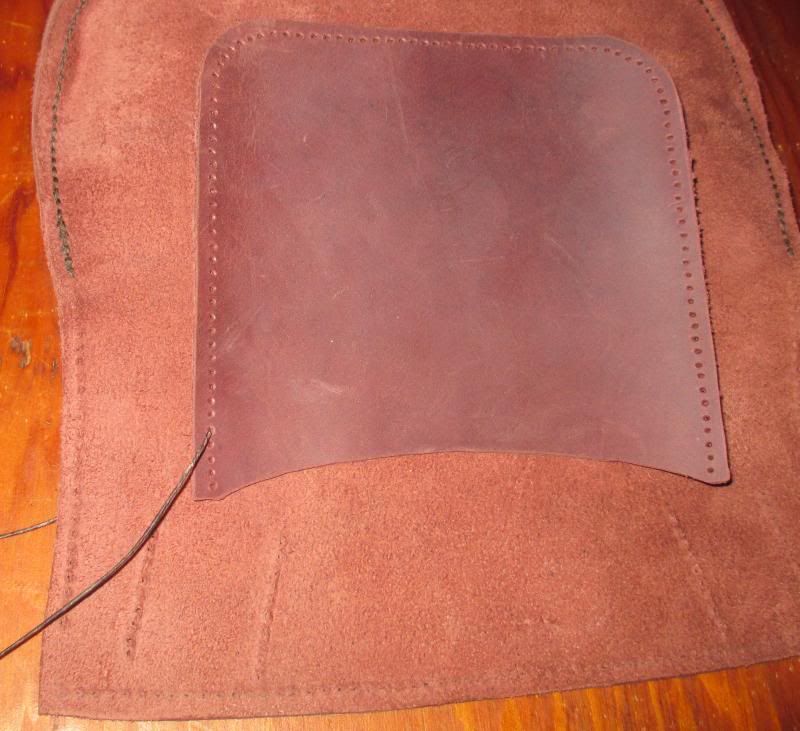
Then, reverse direction and stitch all the way around to the other end. Backstitch 4 or 5 stitches here to lock everything in.
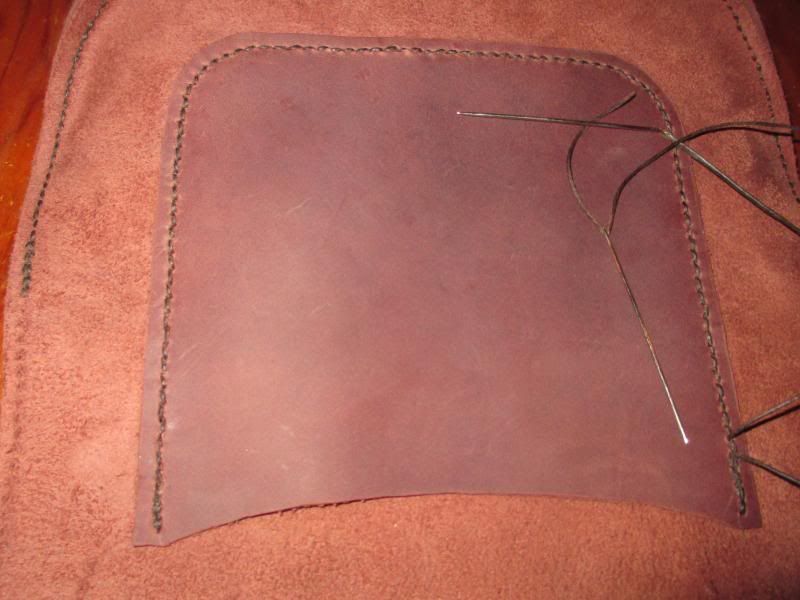
Since the strap is not going to give me any problems on this bag, I'm going to hold off on it for a while yet. It's easier to sew when you don't have to deal with a strap flapping around all over the place.
Now I'll start on the front panel. For this step you will need a strip of welting that is a couple of inches longer than the entire seam around the front panel. Don't cut it short.
The strip of welting should be placed shiny side toward the shiny side of the front panel and the front panel placed shiny side against the shiny side of the back panel. Here again, start at the center of the front panel and the center of the gusset and stitch toward one end of the gusset just like we did earlier.
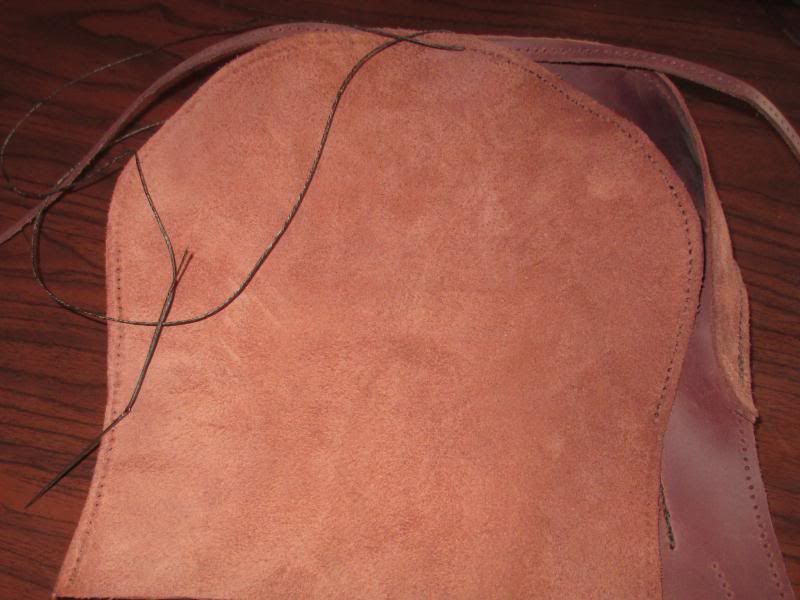
When you get to the end of the gusset, stop and backstitch 4 or 5 stitches to lock it in just like we did on the back panel. Do NOT trim the welt this time.
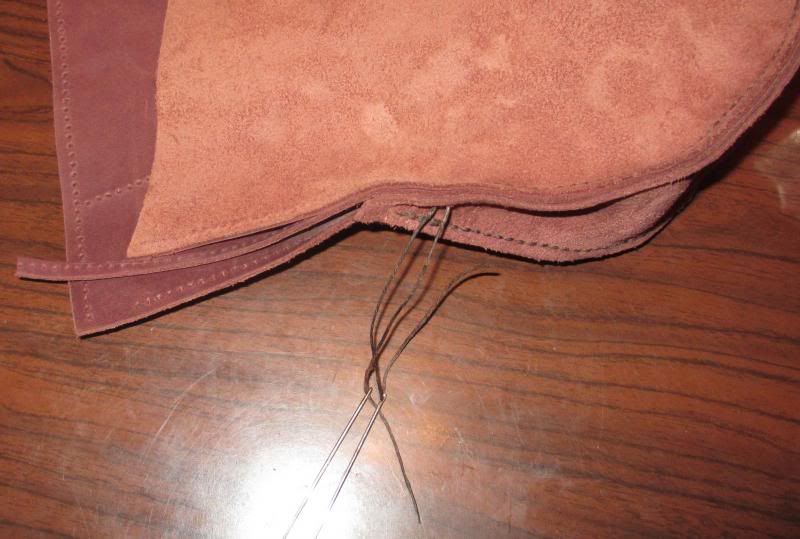
Then stitch the other side the same way starting in the same hole. Backstitch again at this end of the gusset too. Now this thing is really starting to look like a bag!
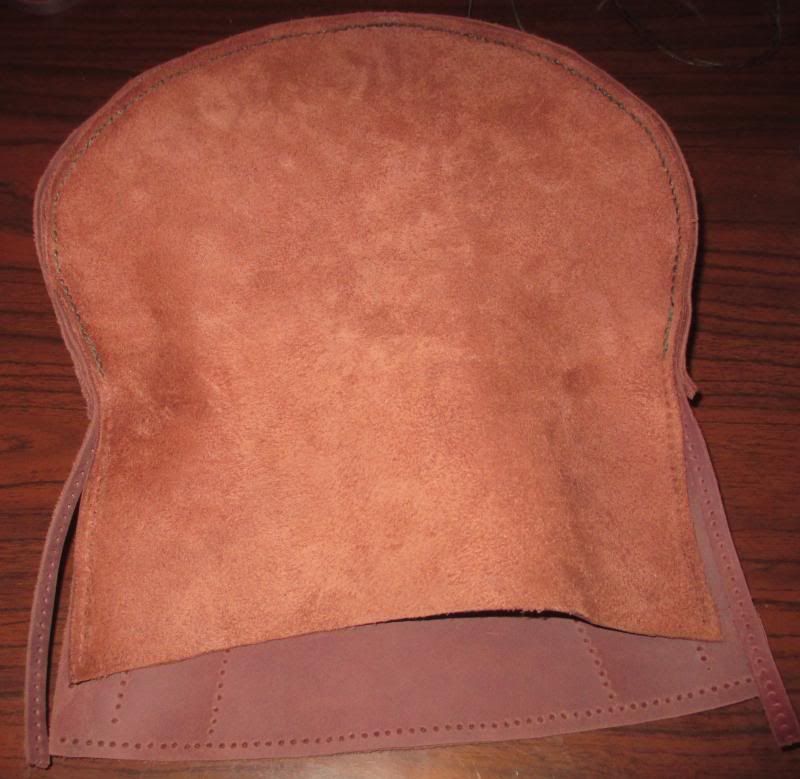
Next installment coming soon.