- Joined
- Nov 26, 2005
- Messages
- 5,229
- Reaction score
- 10,913
Hi,
More done. I cleaned up a lot of the cast parts today. Kind of boring filing and grinding. However, I also installed the other ramrod pipes and the nose cap. Fortunately, the pipes are spaced on the stock properly. The front of the first pipe is 2 7/16" from the front of the nose cap. The front of the middle pipe is 8" and the front of the rear pipe is 15 3/4" from the front of the nose cap. These are measurement from the Morristown gun. The nose cap should be 4 3/8" from the muzzle of the barrel. That provides clearance for the bayonet, which should fit snugly on the barrel with up to 1/4" inch of barrel protruding beyond the socket. The socket is not flush with the muzzle. I will discuss that later, and how to properly fit a bayonet that is meant to function in battle rather than being a reenactor's prop.
The machine inlets for the pipes are located correctly but the mortising work is sloppy. Apparently, the cutters dive into the wood at an angle leaving behind chamfered edges to the mortise. That would be fine if the chamfer begins at the edge of the pipe but the edge is located where the cutter reaches full depth. So now you have a sloping gap at either end of the pipe. TRS is not the only stock maker guilty of this. I've had two other recent precarved stocks from a highly esteemed company that had the same flaws. I have to say that today, the only manufacturer of stocks that can reliably produce truly precise fit of parts is Jim Kibler. Anyway, I have to work with what I have and it will be fine in the end.
Here you can see the gap in front of the pipe caused by the machine cutter.
I will bed the damn things in AcraGlas to fill in the voids and they will disappear. Anyway, first I clean up the castings and I always countersink the mouths of the pipe to prevent a sharp edge scraping the ramrod. Just a little extra thing I routinely do.
The forward pipes on Fergusons have two pins and two separate tabs. So I cut and form those tabs before inletting. I draw a center line down the machine inlet and mark the lengths of each tab.
I don't waste time with "machinist" measurements for this. Just eyeball it. Then I mark the extent of the tabs and punch holes for drilling. After drilling the holes, I cut the edges of the slots with flat chisels and then use my thin slot saw to cut between the holes. I clean up the slots until the pipe can fit down on the wood.
Now I can trace the pipe and set it in in a few minutes using gouges.
The front and rear gaps are small but will be filled. Next, I installed the nose cap. I cut the front of the stock to the correct length and measure a line for the edge of the nose cap using a square. Then I just cut along that line with a Japanese saw, and fit the cap using inletting black. It goes fast.
Bingo Badda Boop and it is all done. That is my new catch phrase for a job well done. It combines "bingo" with "baada bing badda boom", with Bette Boop's famous sign off. It combines a whole lot of old white geezer stuff.
dave
More done. I cleaned up a lot of the cast parts today. Kind of boring filing and grinding. However, I also installed the other ramrod pipes and the nose cap. Fortunately, the pipes are spaced on the stock properly. The front of the first pipe is 2 7/16" from the front of the nose cap. The front of the middle pipe is 8" and the front of the rear pipe is 15 3/4" from the front of the nose cap. These are measurement from the Morristown gun. The nose cap should be 4 3/8" from the muzzle of the barrel. That provides clearance for the bayonet, which should fit snugly on the barrel with up to 1/4" inch of barrel protruding beyond the socket. The socket is not flush with the muzzle. I will discuss that later, and how to properly fit a bayonet that is meant to function in battle rather than being a reenactor's prop.
The machine inlets for the pipes are located correctly but the mortising work is sloppy. Apparently, the cutters dive into the wood at an angle leaving behind chamfered edges to the mortise. That would be fine if the chamfer begins at the edge of the pipe but the edge is located where the cutter reaches full depth. So now you have a sloping gap at either end of the pipe. TRS is not the only stock maker guilty of this. I've had two other recent precarved stocks from a highly esteemed company that had the same flaws. I have to say that today, the only manufacturer of stocks that can reliably produce truly precise fit of parts is Jim Kibler. Anyway, I have to work with what I have and it will be fine in the end.
Here you can see the gap in front of the pipe caused by the machine cutter.
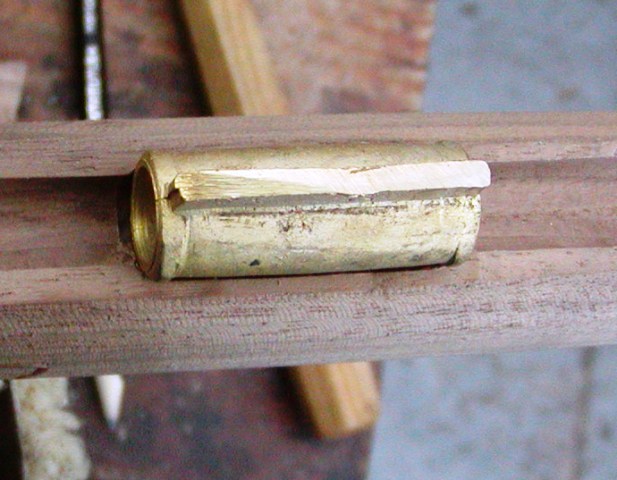
I will bed the damn things in AcraGlas to fill in the voids and they will disappear. Anyway, first I clean up the castings and I always countersink the mouths of the pipe to prevent a sharp edge scraping the ramrod. Just a little extra thing I routinely do.
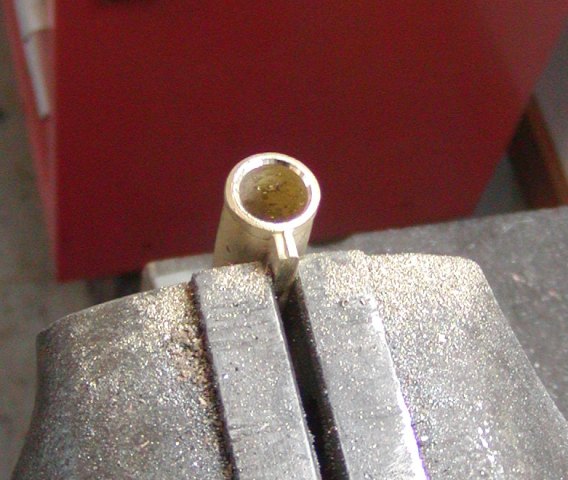
The forward pipes on Fergusons have two pins and two separate tabs. So I cut and form those tabs before inletting. I draw a center line down the machine inlet and mark the lengths of each tab.
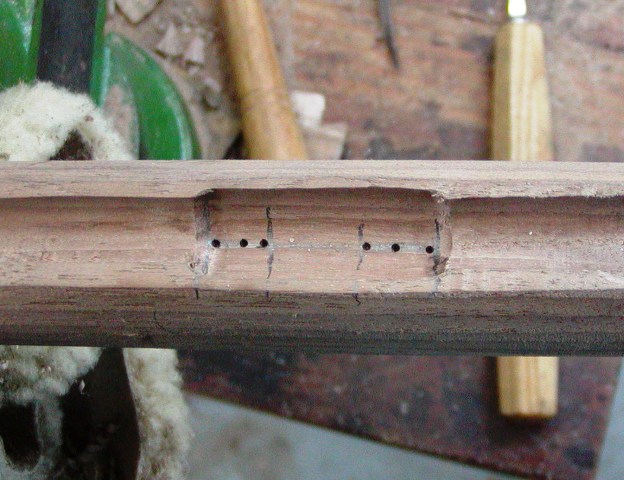
I don't waste time with "machinist" measurements for this. Just eyeball it. Then I mark the extent of the tabs and punch holes for drilling. After drilling the holes, I cut the edges of the slots with flat chisels and then use my thin slot saw to cut between the holes. I clean up the slots until the pipe can fit down on the wood.

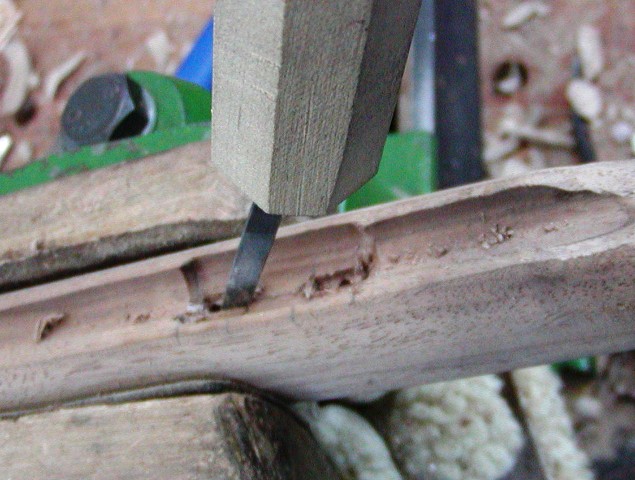
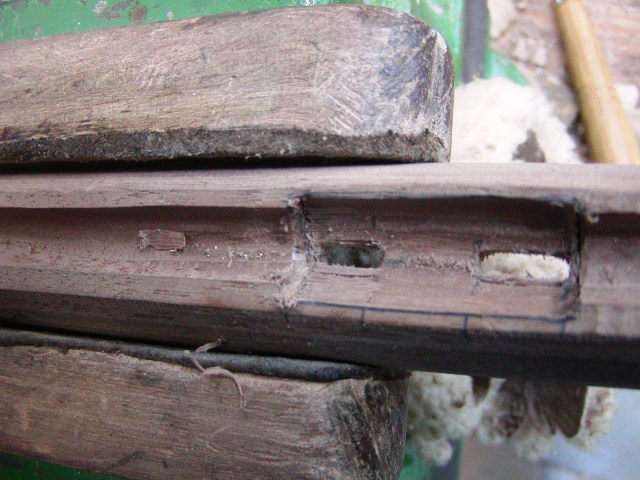
Now I can trace the pipe and set it in in a few minutes using gouges.
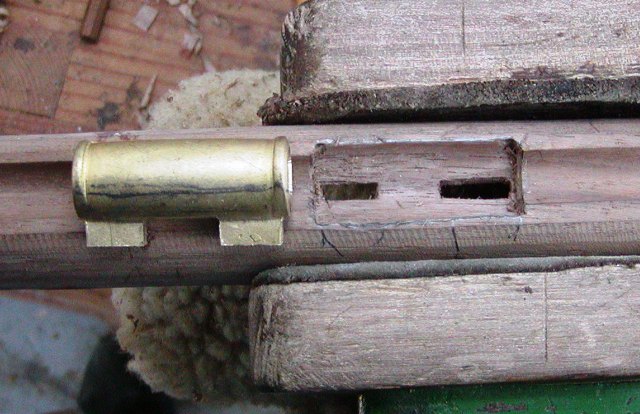
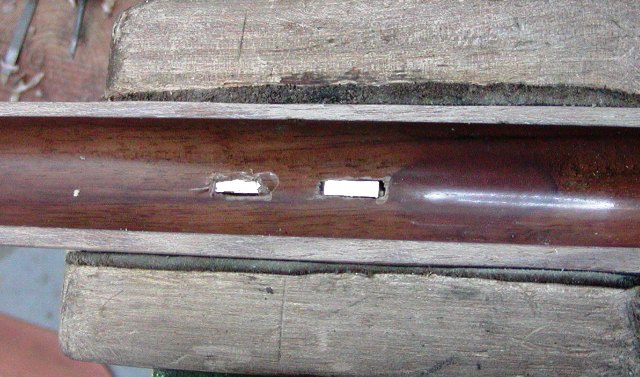
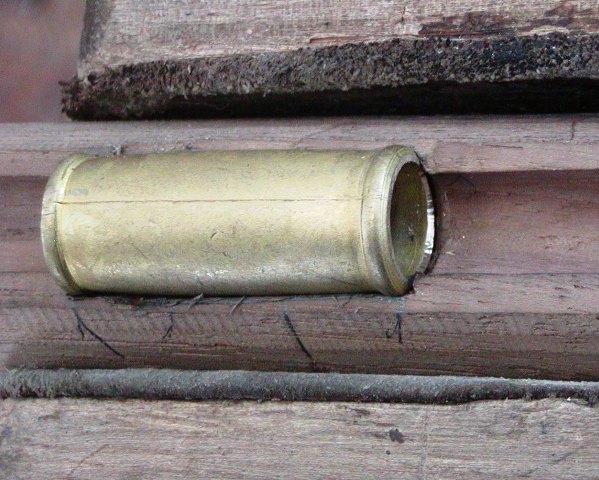
The front and rear gaps are small but will be filled. Next, I installed the nose cap. I cut the front of the stock to the correct length and measure a line for the edge of the nose cap using a square. Then I just cut along that line with a Japanese saw, and fit the cap using inletting black. It goes fast.
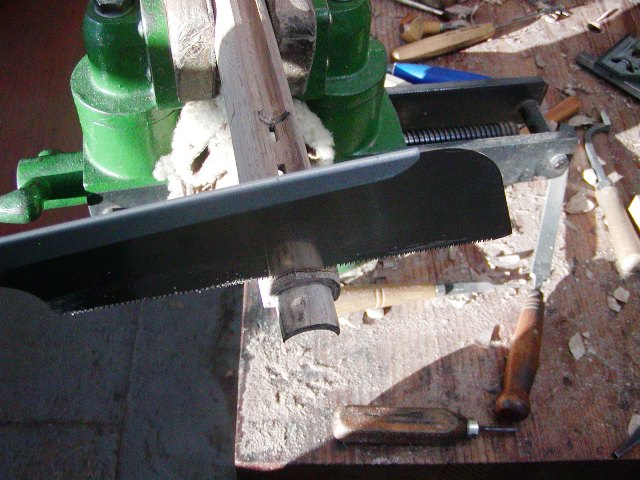
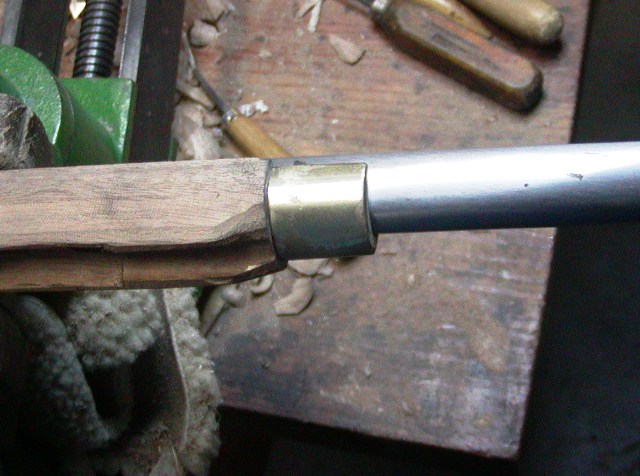
Bingo Badda Boop and it is all done. That is my new catch phrase for a job well done. It combines "bingo" with "baada bing badda boom", with Bette Boop's famous sign off. It combines a whole lot of old white geezer stuff.
dave