Gents:
I have a small dilemma.
My circa 1680s Club Butt fowler that I acquired ”˜used’, is just not reliable for ignition. After a good soaking with Kroil, a solid bench vise, and a large wrench ”¦ I got the breech plug out.
Problem: As you can see, the drilled touch hole (TH) actually interferes right on top of the last thread (not fully formed) of the plug. If/when I picked the TH, the vent pick would not enter the barrel straight, or perpendicular, but would take a large angle towards the muzzle. Between that and miss-fires, even when primed with 4Fg and picked, and I knew I had to do something.
Goal: Since I have it all apart, I’d like to add a Chambers White Lightning TH liner. Either way, with a WL liner or not, even if I file/grind/polish a “groove” into the face of the breech plug as was done with early real arms from yesteryear ”¦ I’ve been told I should be concerned with water from cleaning seeping down into the barrel threads, where either the WL liner or proposed groove is cut away from the existing breech plug top edge surface.
What do I do to prevent that from being a real concern? I have the best thread anti-siezing compounds available on hand:
- Tef-Gel (FANTASTIC for stainless steels!)
-Permatex nickel and copper-based anti-sieze compounds
-Triple Guard, a blue-colored waterproof fully synthetic grease (I use this extensively on boats [my otha’ hobby!] and it doesn’t break down even with saltwater immersion and actually still protects even when ”˜mixed’ at a ratio of 75% grease to 25% saltwater)
-OMC gasket sealing compound, probably made by Permatex (I use this on OB motor lower unit bolts immersed in saltwater and I’ve never failed to remove a bolt even after years of saltwater use ”¦ and have done this successfully on dozens of motors for 40+ years)
Plan: What I’d like to do is tap/thread the barrel for the WL liner, using my drill press with mill vise so I know I can get a perfect tight cut and full threadform. I intend to thread the plug in fully greased and lubed with CLP (as I WILL remove it, possibly a few times) and then fit the Chambers WL liner.
I guess what I’m alluding to, is where the plug threads will “hit” the WL liner - do I grind away some of the breech plug (like the proposed groove) or do I surgically remove some of the WL liner threads? Whereas some of the WL liner will behind the face of the breech plug, I believe I should leave as much of the WL liner threads intact, no?
With all that ”¦ I remain VERY curious what to do whereas I have a well-breeched plug LESS the existing TH location is right at the face of the plug, which means it is already centered on the pan placement as is. Personally I think the builder should have set the breeched barrel back another 1/8” or so to move the TH a tad forward.
Also interested in comments on the THE best thread goop to use.
Cheers!
I have a small dilemma.
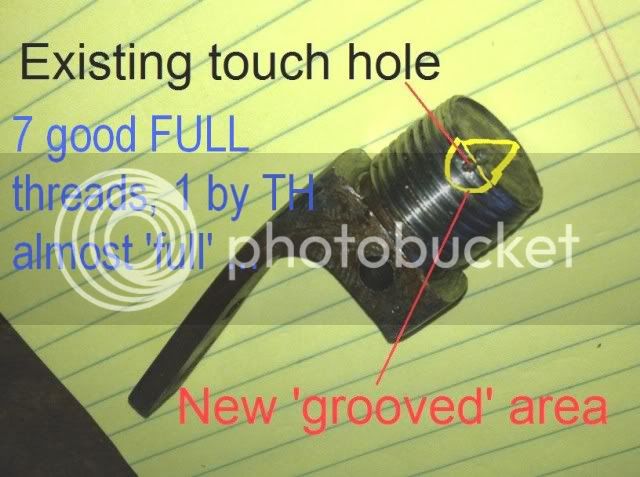
My circa 1680s Club Butt fowler that I acquired ”˜used’, is just not reliable for ignition. After a good soaking with Kroil, a solid bench vise, and a large wrench ”¦ I got the breech plug out.
Problem: As you can see, the drilled touch hole (TH) actually interferes right on top of the last thread (not fully formed) of the plug. If/when I picked the TH, the vent pick would not enter the barrel straight, or perpendicular, but would take a large angle towards the muzzle. Between that and miss-fires, even when primed with 4Fg and picked, and I knew I had to do something.
Goal: Since I have it all apart, I’d like to add a Chambers White Lightning TH liner. Either way, with a WL liner or not, even if I file/grind/polish a “groove” into the face of the breech plug as was done with early real arms from yesteryear ”¦ I’ve been told I should be concerned with water from cleaning seeping down into the barrel threads, where either the WL liner or proposed groove is cut away from the existing breech plug top edge surface.
What do I do to prevent that from being a real concern? I have the best thread anti-siezing compounds available on hand:
- Tef-Gel (FANTASTIC for stainless steels!)
-Permatex nickel and copper-based anti-sieze compounds
-Triple Guard, a blue-colored waterproof fully synthetic grease (I use this extensively on boats [my otha’ hobby!] and it doesn’t break down even with saltwater immersion and actually still protects even when ”˜mixed’ at a ratio of 75% grease to 25% saltwater)
-OMC gasket sealing compound, probably made by Permatex (I use this on OB motor lower unit bolts immersed in saltwater and I’ve never failed to remove a bolt even after years of saltwater use ”¦ and have done this successfully on dozens of motors for 40+ years)
Plan: What I’d like to do is tap/thread the barrel for the WL liner, using my drill press with mill vise so I know I can get a perfect tight cut and full threadform. I intend to thread the plug in fully greased and lubed with CLP (as I WILL remove it, possibly a few times) and then fit the Chambers WL liner.
I guess what I’m alluding to, is where the plug threads will “hit” the WL liner - do I grind away some of the breech plug (like the proposed groove) or do I surgically remove some of the WL liner threads? Whereas some of the WL liner will behind the face of the breech plug, I believe I should leave as much of the WL liner threads intact, no?
With all that ”¦ I remain VERY curious what to do whereas I have a well-breeched plug LESS the existing TH location is right at the face of the plug, which means it is already centered on the pan placement as is. Personally I think the builder should have set the breeched barrel back another 1/8” or so to move the TH a tad forward.
Also interested in comments on the THE best thread goop to use.
Cheers!