- Joined
- Nov 26, 2005
- Messages
- 5,212
- Reaction score
- 10,836
Hi Guys,
Well, I had to make a correction. I was so focused on the dimensions of the original gun that I failed to adapt the stock to the dimensions of my client. Based on his handling some rifles in my shop, he needed about 3/8" more drop at heel (of the butt plate) than the original gun. I already band sawed out the stock based on the original so what to do. Well here is the solution. This shows why I love my bench and vise arrangement. I clamped the stock in my one of my wooden leg vises and fitted a pipe clamp anchored by a dog in one of my bench holes. That provided the force for bending. Then I wrapped the wrist of the stock with an old sock secured with twine. I heated canola oil to the point of smoking and ladled it on to the sock. When the wood was saturated with the oil on the surface, I applied pressure to the pipe clamp until I'd added about 1/2" of drop to the stock. After the oil cooled, I released the clamp and he stock rebounded to a shape with 3/8" more drop. I bet no one has shown you guys this trick before.
dave
Well, I had to make a correction. I was so focused on the dimensions of the original gun that I failed to adapt the stock to the dimensions of my client. Based on his handling some rifles in my shop, he needed about 3/8" more drop at heel (of the butt plate) than the original gun. I already band sawed out the stock based on the original so what to do. Well here is the solution. This shows why I love my bench and vise arrangement. I clamped the stock in my one of my wooden leg vises and fitted a pipe clamp anchored by a dog in one of my bench holes. That provided the force for bending. Then I wrapped the wrist of the stock with an old sock secured with twine. I heated canola oil to the point of smoking and ladled it on to the sock. When the wood was saturated with the oil on the surface, I applied pressure to the pipe clamp until I'd added about 1/2" of drop to the stock. After the oil cooled, I released the clamp and he stock rebounded to a shape with 3/8" more drop. I bet no one has shown you guys this trick before.
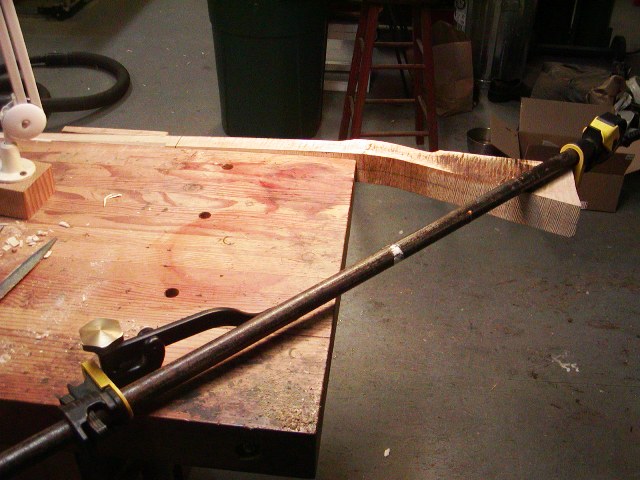
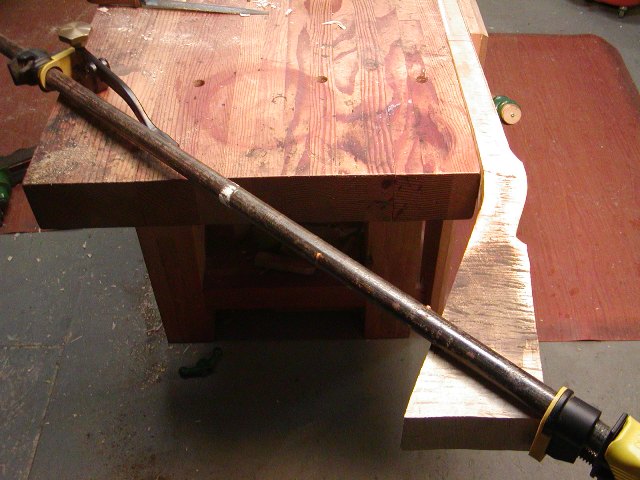
dave