- Joined
- Nov 26, 2005
- Messages
- 5,224
- Reaction score
- 10,884
Hi,
I am building as close a copy of the Marshall rifle as I can without having the original on my bench. I've examined the original rifle and have a large photo library of images to work from as well as Houston Harrison's excellent drawings. The first problem is the lock. No one makes the right lock. All the locks sold with EM rifle kits are too large and have curved plates. They make it impossible to capture the look of the original. So, I had to make a lock. The best choice for size and shape was M&G's "Albrecht" lock. I had low expectations and wasn't disappointed. It was good raw material but needed a lot of work.
Hear is a photo of the original lock.
The first task was adding a pan bridle, which I welded on and shaped.
Next I had to drill it for the frizzen and mount a screw from the inside of the lock plate. That meant filling the old hole in the frizzen and drilling and fitting everything. It came out well.
The original lock has a blind hole tapped for the rear lock bolt. For some reason , M&G ground away most of the bolster where that screw goes so I filled it with weld. I also added weld to fatten the tail of the plate and filed the nose to the shape of the original.
Then I had to clean up the plate and all the parts, reshape the flint **** and frizzen, and cut the border on the plate and flint ****.
Finally, I worked over the springs, reshaped the finial on the frizzen spring, fitted a high carbon sole on the frizzen to add mass, fitted and polished all the parts, heat treated everything, and engraved the lock as close to the original as I could.
The lock now has a wonderful feel, smooth, silky action, and sparks like crazy.
dave
I am building as close a copy of the Marshall rifle as I can without having the original on my bench. I've examined the original rifle and have a large photo library of images to work from as well as Houston Harrison's excellent drawings. The first problem is the lock. No one makes the right lock. All the locks sold with EM rifle kits are too large and have curved plates. They make it impossible to capture the look of the original. So, I had to make a lock. The best choice for size and shape was M&G's "Albrecht" lock. I had low expectations and wasn't disappointed. It was good raw material but needed a lot of work.
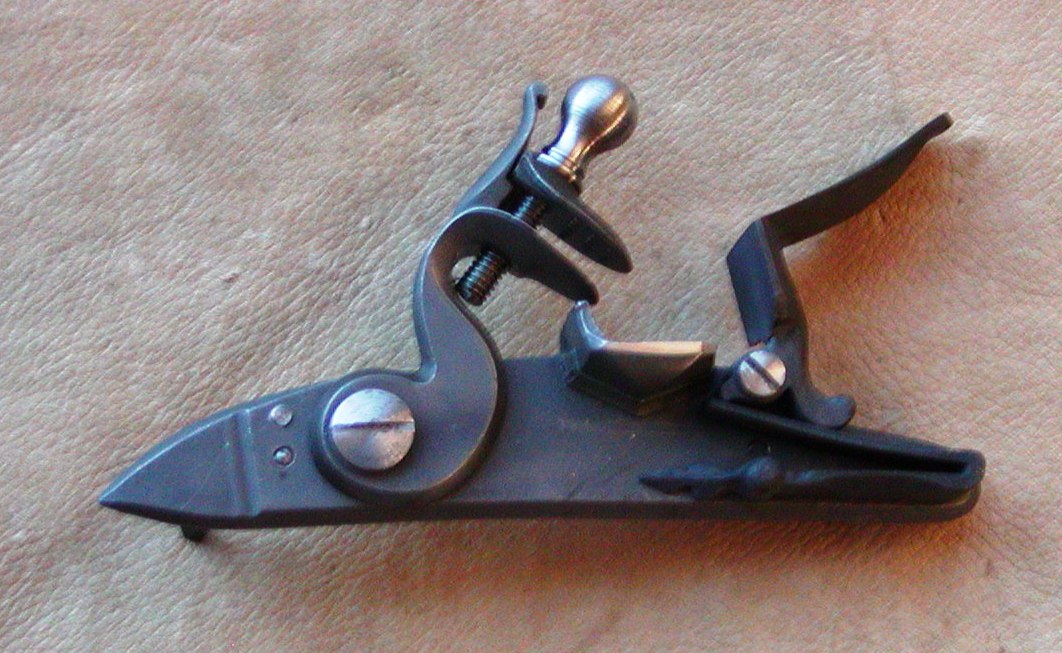
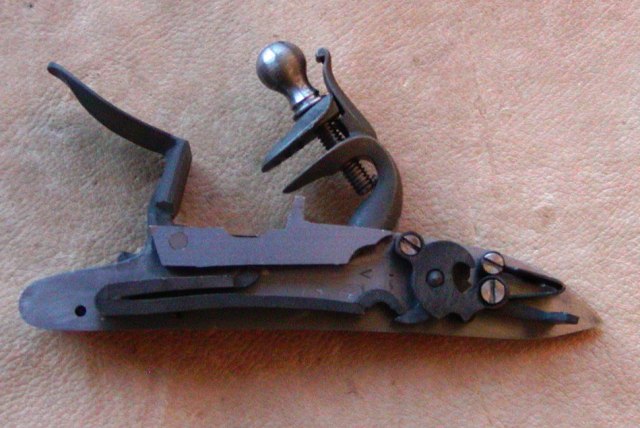
Hear is a photo of the original lock.
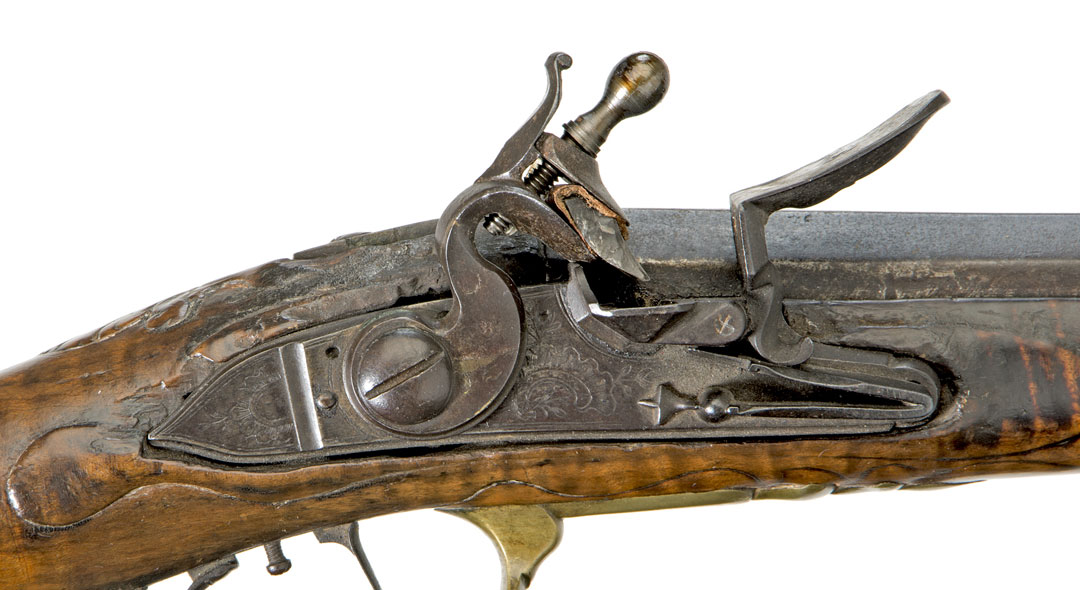
The first task was adding a pan bridle, which I welded on and shaped.
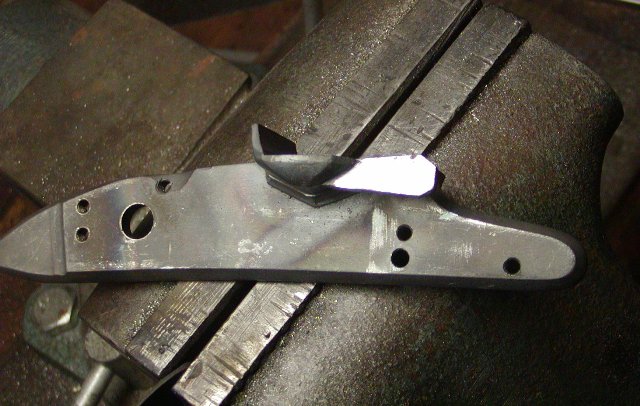
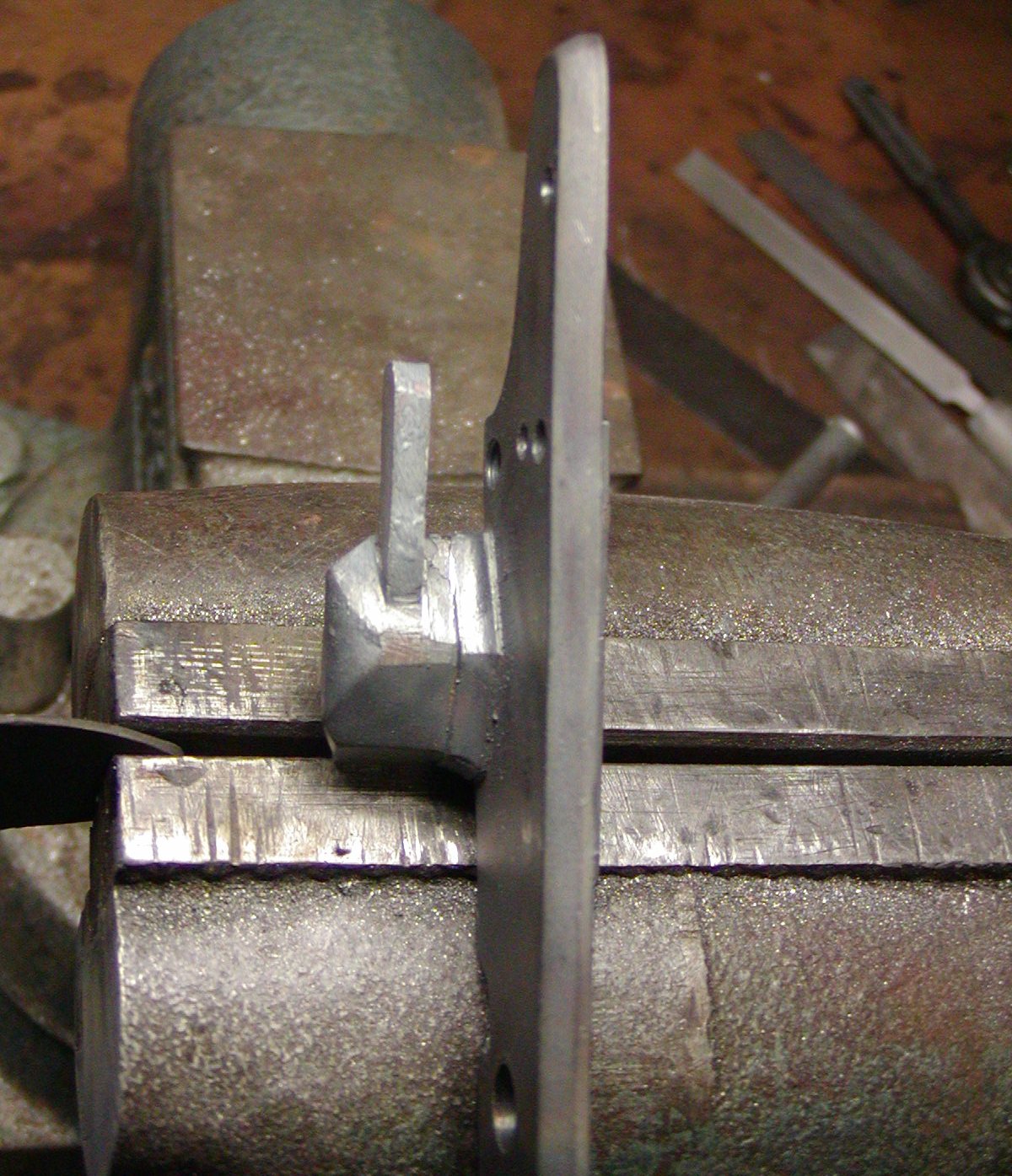
Next I had to drill it for the frizzen and mount a screw from the inside of the lock plate. That meant filling the old hole in the frizzen and drilling and fitting everything. It came out well.
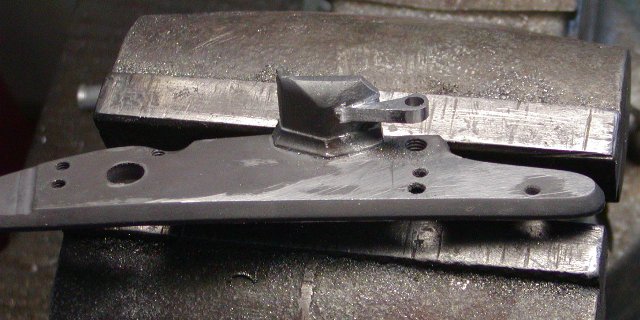
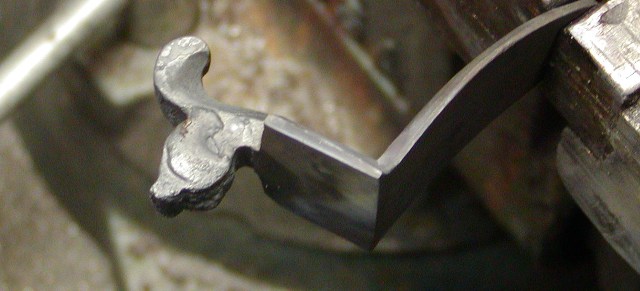
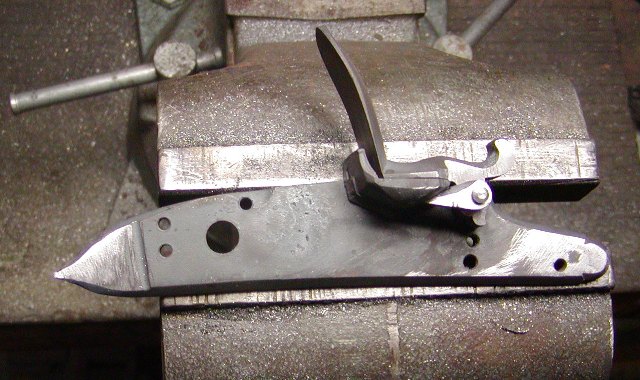
The original lock has a blind hole tapped for the rear lock bolt. For some reason , M&G ground away most of the bolster where that screw goes so I filled it with weld. I also added weld to fatten the tail of the plate and filed the nose to the shape of the original.
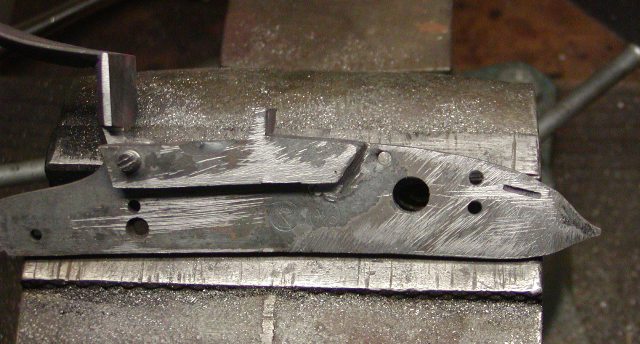
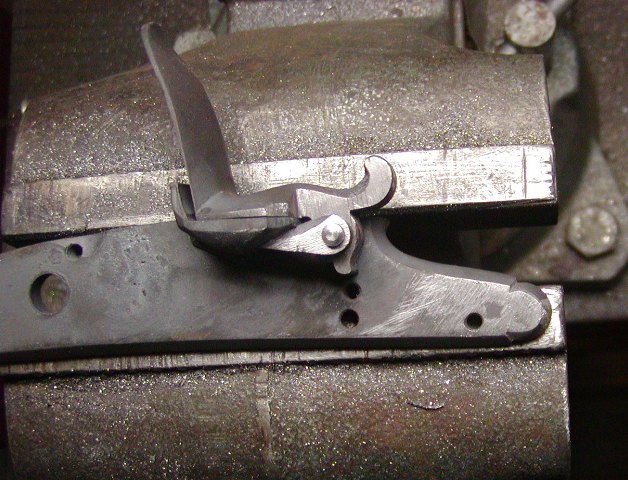
Then I had to clean up the plate and all the parts, reshape the flint **** and frizzen, and cut the border on the plate and flint ****.
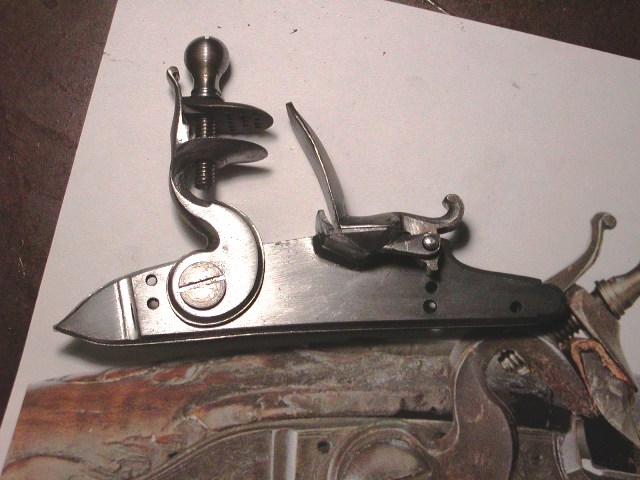
Finally, I worked over the springs, reshaped the finial on the frizzen spring, fitted a high carbon sole on the frizzen to add mass, fitted and polished all the parts, heat treated everything, and engraved the lock as close to the original as I could.
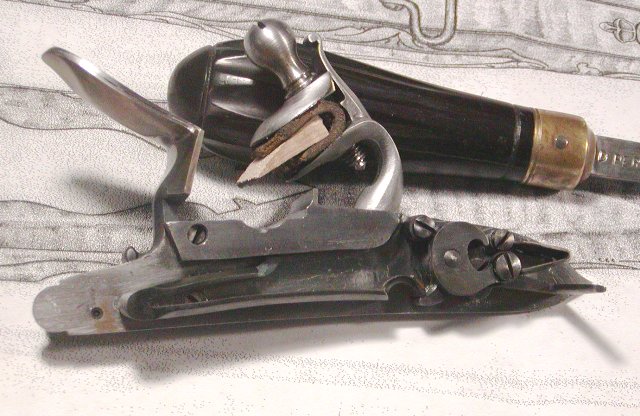
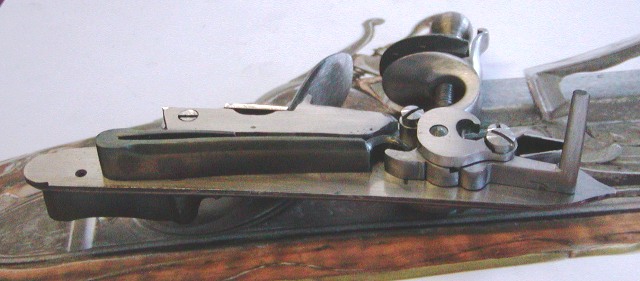
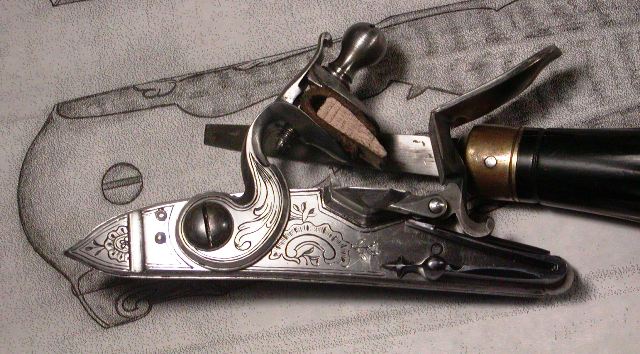
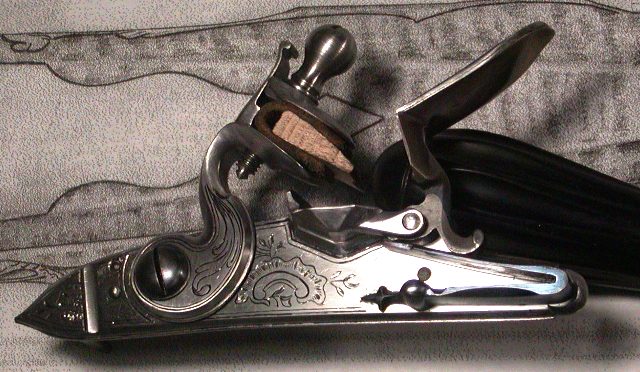
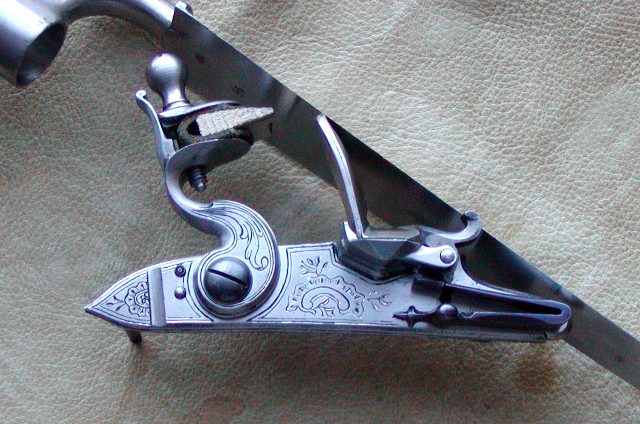
The lock now has a wonderful feel, smooth, silky action, and sparks like crazy.
dave