Hello,
I am attempting to make a reproduction Hudson Bay Trade knife for a friend of mine. I found a couple of sketches on-line, but they didn't seem to follow the photos of originals that I found. I am guessing that there were different companies that made these which could explain the variances.
In any event I decided to use some images of a couple different Jukes Coulson trade knifes for reference and modeled them in CAD to create a drawing to use for reference, but I am still not sure that I have it. I have attached what I have right now and would welcome any comments you might have.
Overall length on this one is about 13.5 inches and it is about 1/4 inch thick at the spine. One source says that the bolsters and washers are 1/16 inch thick brass. I could see that for the washers, but the bolsters on some photographs look to be thicker, perhaps 1/8 inch. The pins on some photos look to be brass, but on others they look to be iron. The other area of question is the ricasso above the bolster. On some photos it looks to be non-existent on the left side, but there on the right. Seems like an odd configuration to me, but it is difficult to tell in the ones that I have seen online. Handles appear to be horn, but they could also be walnut or some other darker wood. In any event, have a look.
I am attempting to make a reproduction Hudson Bay Trade knife for a friend of mine. I found a couple of sketches on-line, but they didn't seem to follow the photos of originals that I found. I am guessing that there were different companies that made these which could explain the variances.
In any event I decided to use some images of a couple different Jukes Coulson trade knifes for reference and modeled them in CAD to create a drawing to use for reference, but I am still not sure that I have it. I have attached what I have right now and would welcome any comments you might have.
Overall length on this one is about 13.5 inches and it is about 1/4 inch thick at the spine. One source says that the bolsters and washers are 1/16 inch thick brass. I could see that for the washers, but the bolsters on some photographs look to be thicker, perhaps 1/8 inch. The pins on some photos look to be brass, but on others they look to be iron. The other area of question is the ricasso above the bolster. On some photos it looks to be non-existent on the left side, but there on the right. Seems like an odd configuration to me, but it is difficult to tell in the ones that I have seen online. Handles appear to be horn, but they could also be walnut or some other darker wood. In any event, have a look.
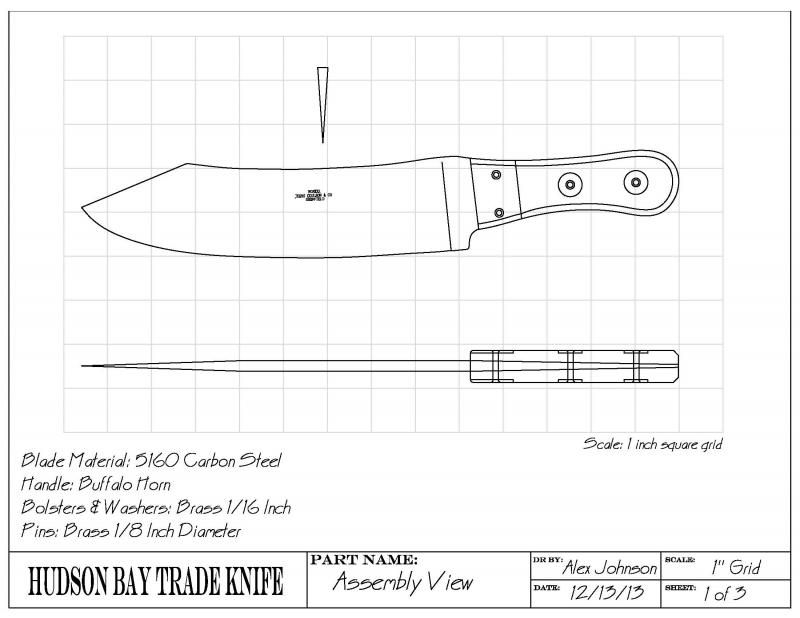