GANGGREEN
45 Cal.
This photo is a bit misleading because I had to take it at a downward angle so that you could see the touchhole. I'm using a re-purposed barrel with the touchhole already drilled. When I lined up the L&R late English lock to start inletting the lock mortise, I see that it doesn't really line up right (again, the photo looks OK but it's misleading). If I put the nose of the lockplate between the barrel and ramrod channel, the tail sits way to low and if I sit the tail halfway on the wrist, the nose sits too low. Also, the touchhole is apparently going to have to sit inside the pan, lower than flush/horizon level. Now, I suppose that I can drill a new hole slightly higher and install a liner, but that's still not going to totally rectify things.
What am I doing wrong? Am I missing something obvious? As it is, I THINK I'll be able to make this work, but only by adding a liner and moving the touchhole slightly up and by drilling the nose of the lockplate very high. Thoughts?
What am I doing wrong? Am I missing something obvious? As it is, I THINK I'll be able to make this work, but only by adding a liner and moving the touchhole slightly up and by drilling the nose of the lockplate very high. Thoughts?
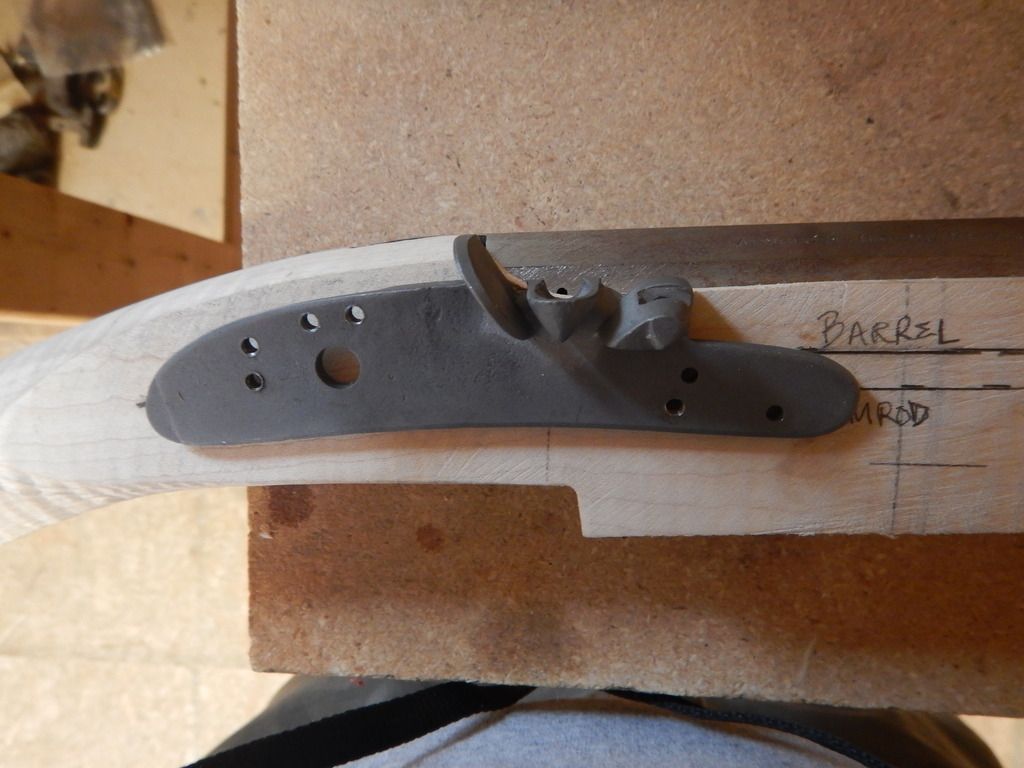