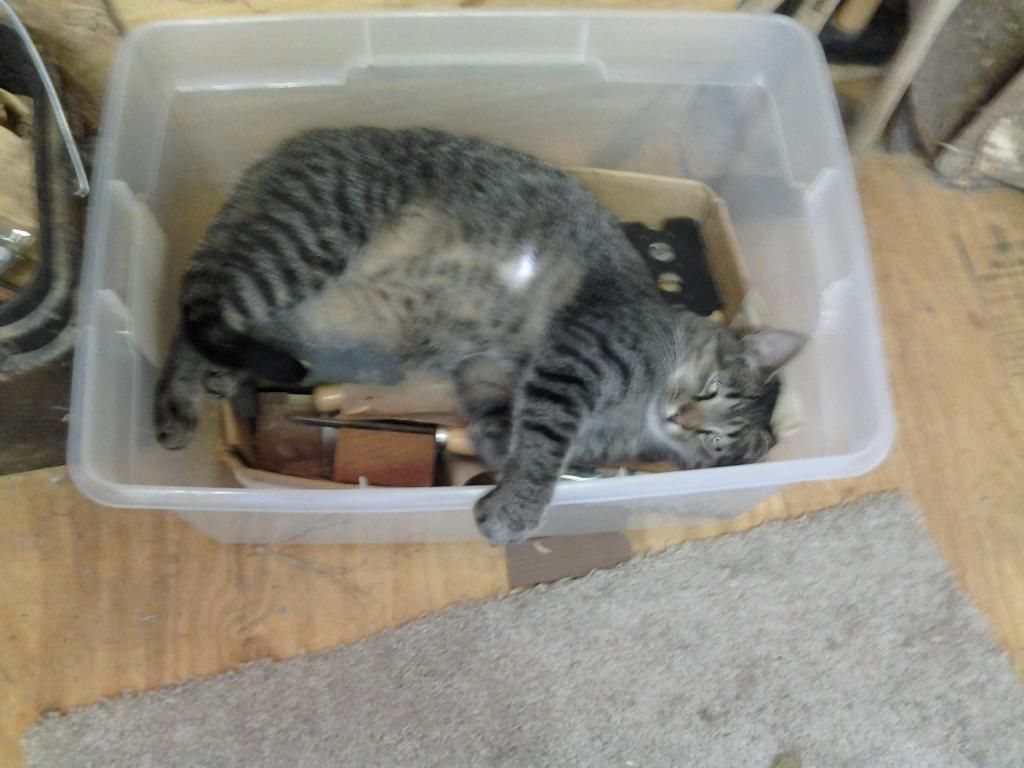
Tomtom and I have been sidetracked with things until today...after visiting Davy Crockett days at the park(not many vendors) i was able to jig up and use 2 flatbar stock to set guide rails for a little Bosche pony router:
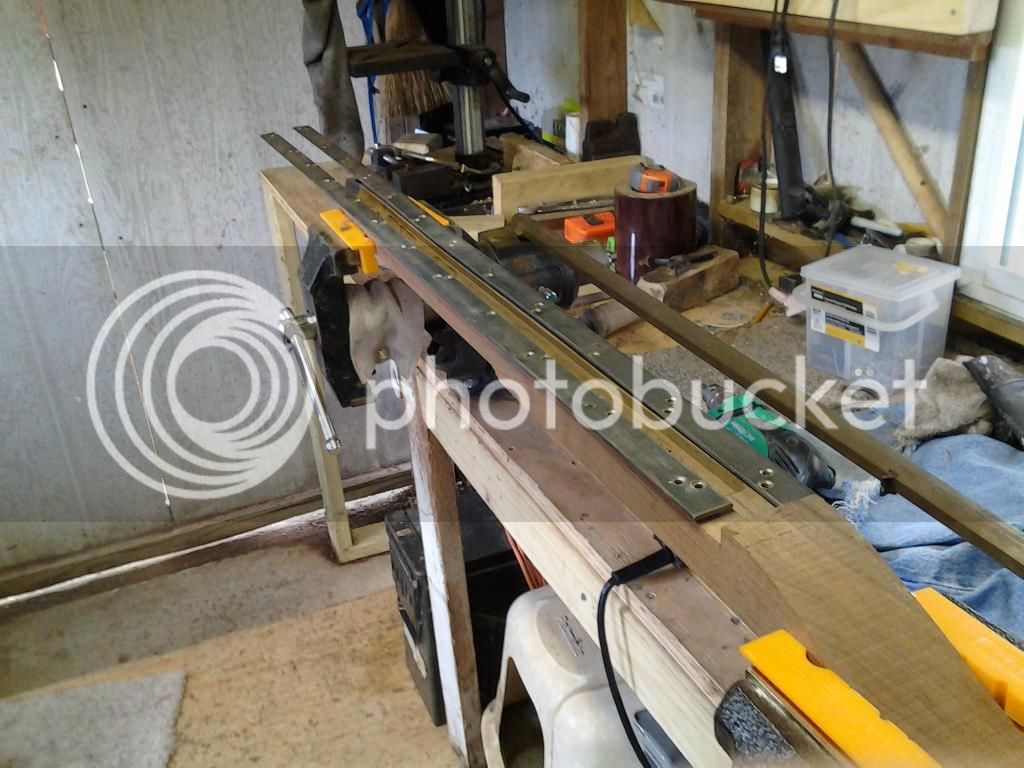
The bars were drilled and coutersunk holes for wood screw flush fit. Washers were placed under each station that held a screw, this was a straight barrel, but if you have a swamped, alter the height by adding or subtracting washers under the screws. then it's very important to adjust the router bit for height and side to side movement...then lock it in the chuck, and route away the wood.
The RR grove was also done, then the short spaces at the ends where you cannot take the router, can be cleaned up with rasps and a chisel.....takes a while to jig up, but NO elbow grease was used in the process....and the walls fit the barrel perfectly......
class over.....go back to napping tomtom says....
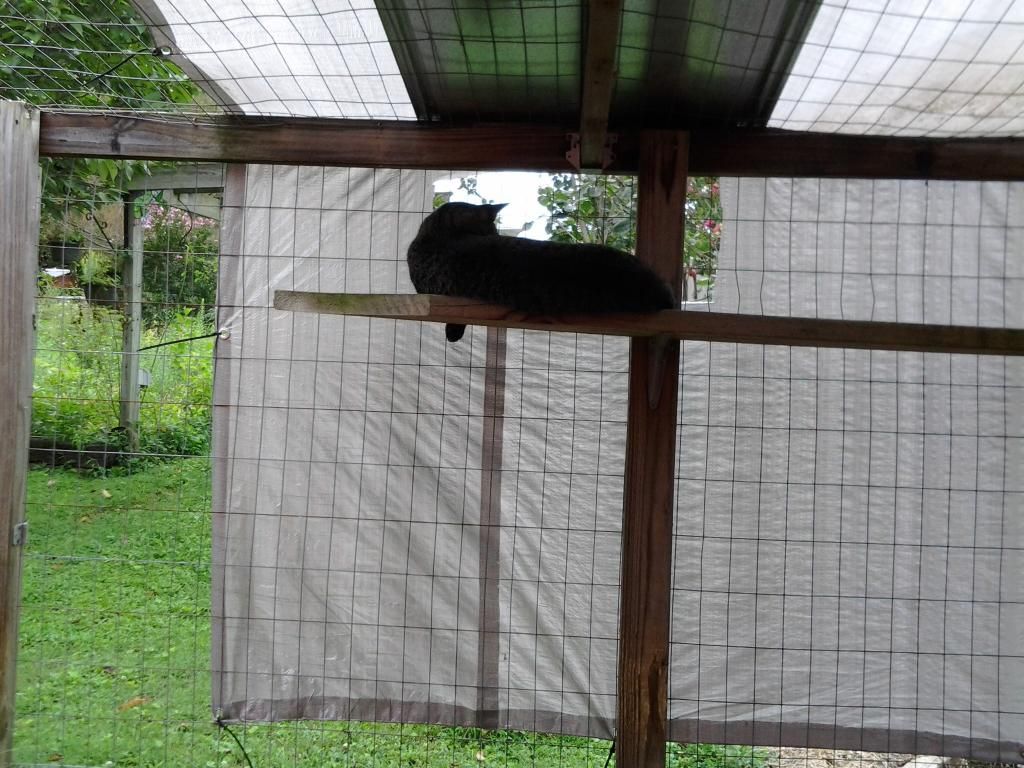
:grin: :bow: