mikemeteor
45 Cal.
- Joined
- Nov 16, 2008
- Messages
- 660
- Reaction score
- 3
still waitin' on the raw materials for my homemade nickel silver nosecap.
ordered from some jewelry joint in Calieforney.
probably a mistake.
so I started carving.
practiced a little on a cherry board, then jumped in.
humbling experience.
here's the rough start.
can't seem to get the 3-D look that I see in all the pictures.
I think when I took down my lockplates, I didn't leave enough for the relief I needed.
- that radius that goes from stock up to lock panel - I'm missing that :shake: !
Either that or I gotta make my wrist a fair amount skinnier - which makes me nervous.
Plus I'm too dang cheap (right now) to get some quality gouges, so I'm doing everything with straight blades.
Another source of self-inflicted frustration.
ordered from some jewelry joint in Calieforney.
probably a mistake.
so I started carving.
practiced a little on a cherry board, then jumped in.
humbling experience.
here's the rough start.
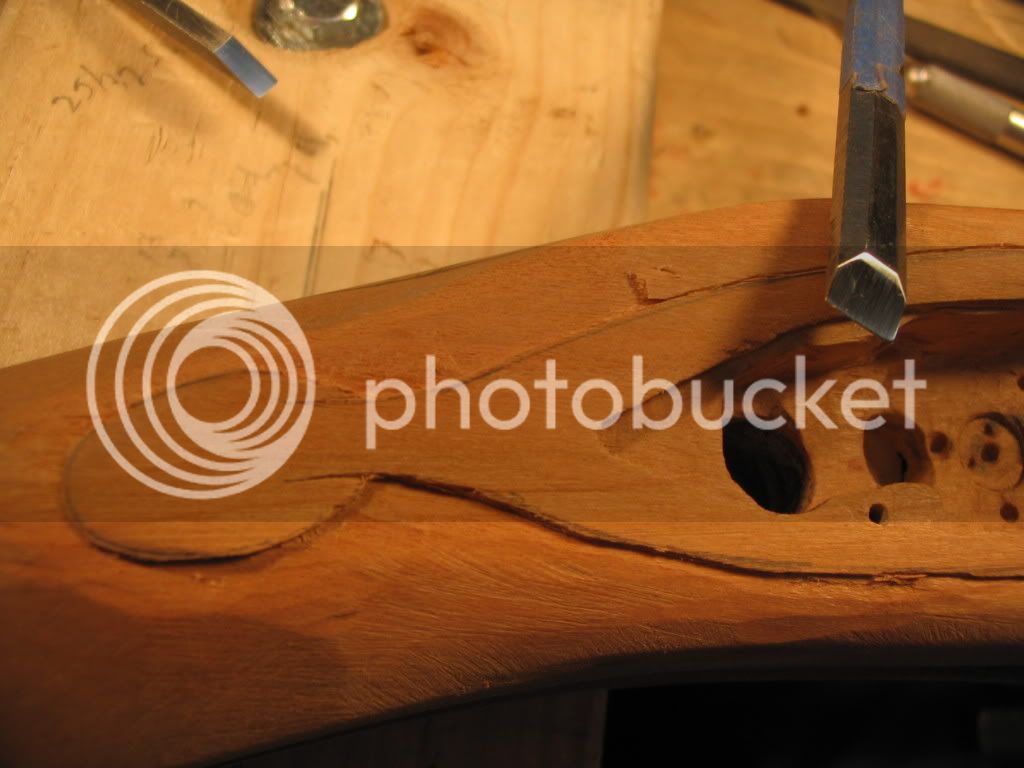
can't seem to get the 3-D look that I see in all the pictures.
I think when I took down my lockplates, I didn't leave enough for the relief I needed.
- that radius that goes from stock up to lock panel - I'm missing that :shake: !
Either that or I gotta make my wrist a fair amount skinnier - which makes me nervous.
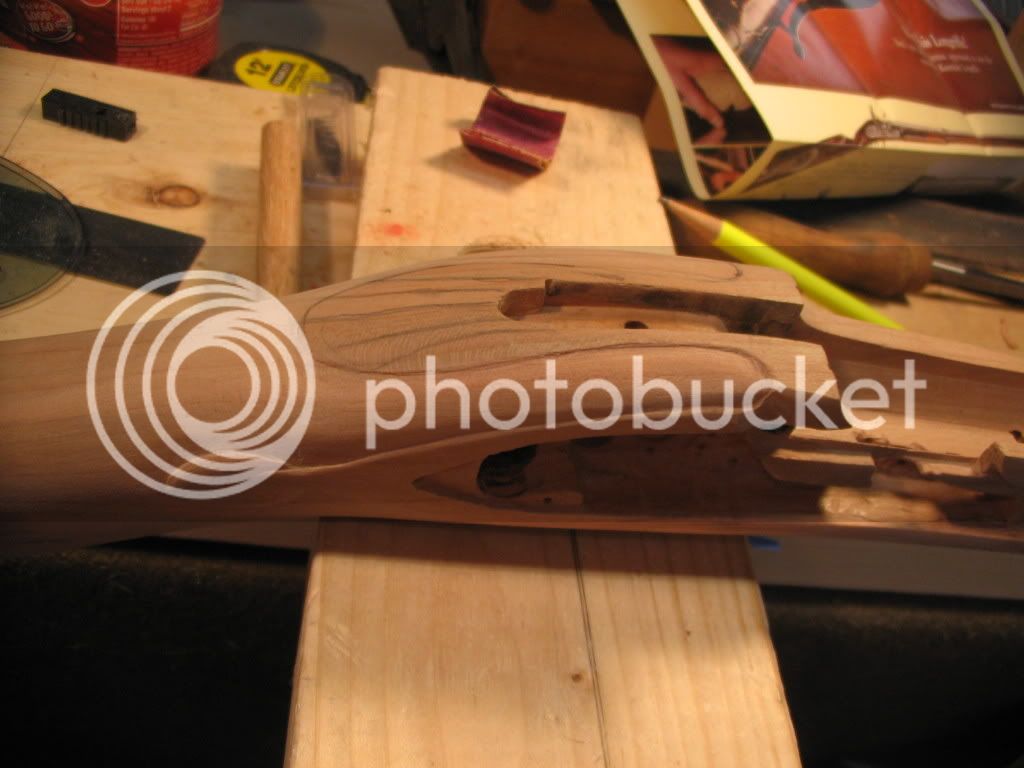
Plus I'm too dang cheap (right now) to get some quality gouges, so I'm doing everything with straight blades.
Another source of self-inflicted frustration.