Progress photos - mainspring support riveted thru lockplate and top of the support riveted on after (side view). The sear will pivot inside this part.
100_0592
View showing mainspring support top rivet - used the 16 oz. machinist hammer this time. You can see that the mainspring bears against the support. I made the part asymmetric.
100_0594
Support top smoothed out.
100_0596
later, Mike (click on the photos & they'll enlarge at flickr)

View showing mainspring support top rivet - used the 16 oz. machinist hammer this time. You can see that the mainspring bears against the support. I made the part asymmetric.
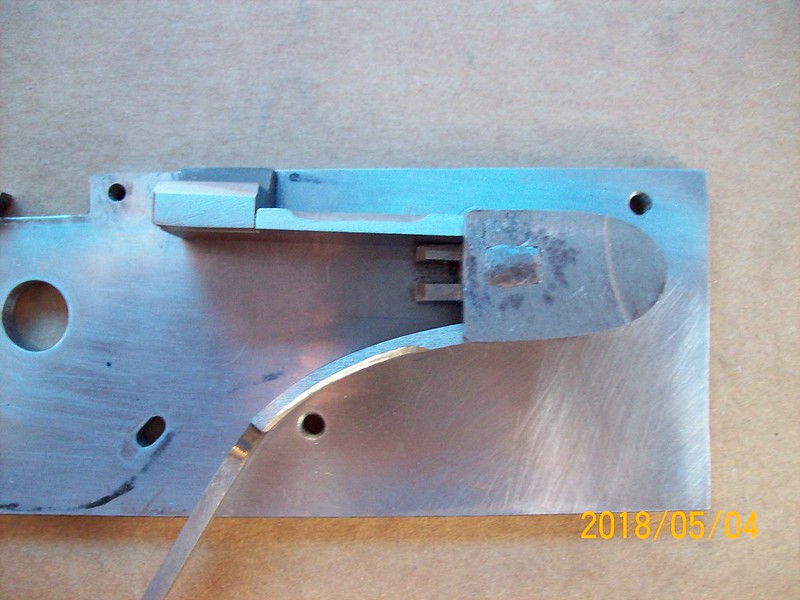
Support top smoothed out.
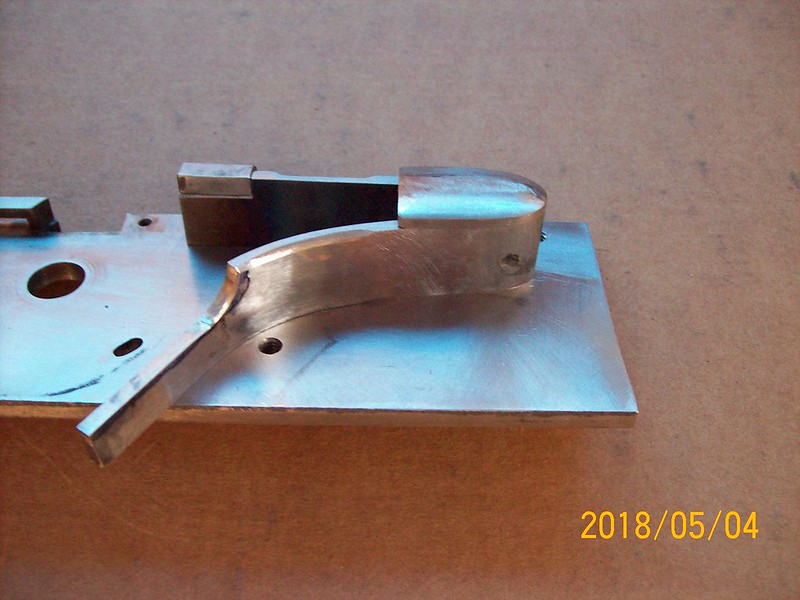
later, Mike (click on the photos & they'll enlarge at flickr)