So, I'm using the broken cast piece to form "dies" out of maple scraps. I've cut the brass sheet (.80) and began to peen it. I will say, this is the first buttcap I've ever done. And I want it a bit deeper or "cup like" so that takes more pounding.
I have discovered that it's not a "fold up the metal" process.....but more of a "push out the shape" process. I'm using a thick brass punch as well as a ball peen hammer and that broken cast piece.
The most use is coming from the brass punch. It seems to push the metal where I'm asking it to go vs a ball peen hammer.
When I laid out the brass sheet for cutting I took the broken piece and "rolled it" from left to right, and front to back to obtain (what I thought) would be the right amount of sheet brass. Well, as the process goes on Im finding out that I'm pushing the brass to form the piece. As such, I'm cutting off more of the metal at the top. In other words, I started out with to much or to big of a brass piece. Right now I've cut off a good 1/4" from each side....yes....a bit more than a half-inch. But....better to have more and not need it, than not enough to finish it.
I'm not done....but closer than when I began this piece.
I have discovered that it's not a "fold up the metal" process.....but more of a "push out the shape" process. I'm using a thick brass punch as well as a ball peen hammer and that broken cast piece.
The most use is coming from the brass punch. It seems to push the metal where I'm asking it to go vs a ball peen hammer.
When I laid out the brass sheet for cutting I took the broken piece and "rolled it" from left to right, and front to back to obtain (what I thought) would be the right amount of sheet brass. Well, as the process goes on Im finding out that I'm pushing the brass to form the piece. As such, I'm cutting off more of the metal at the top. In other words, I started out with to much or to big of a brass piece. Right now I've cut off a good 1/4" from each side....yes....a bit more than a half-inch. But....better to have more and not need it, than not enough to finish it.
I'm not done....but closer than when I began this piece.
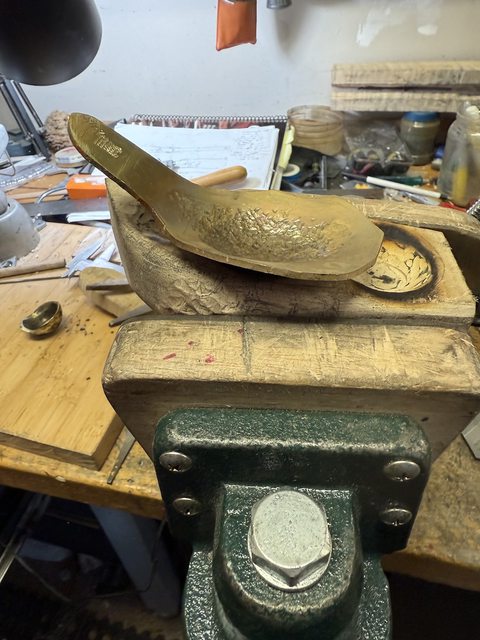
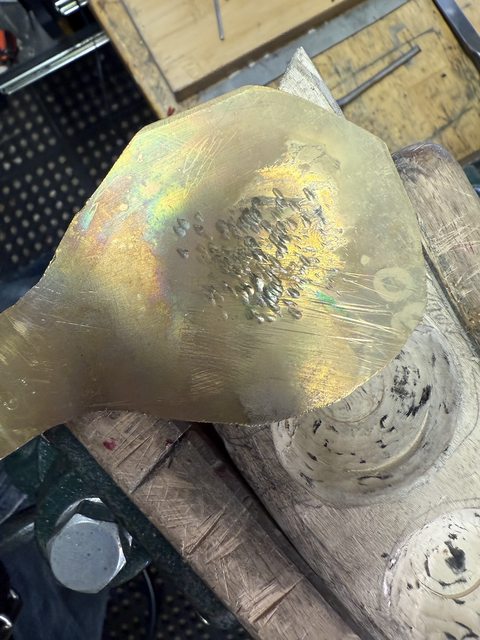
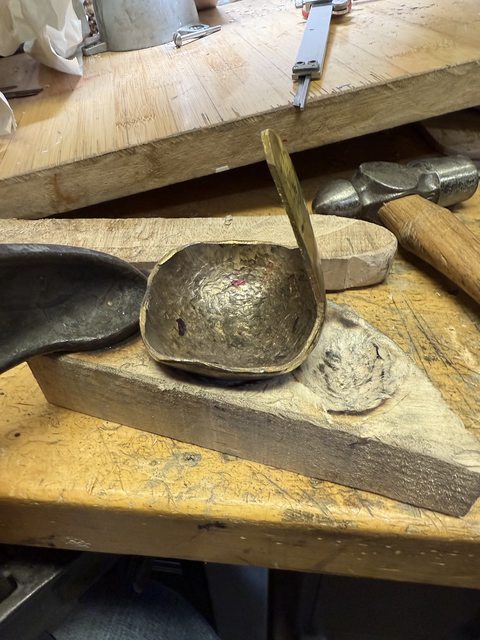
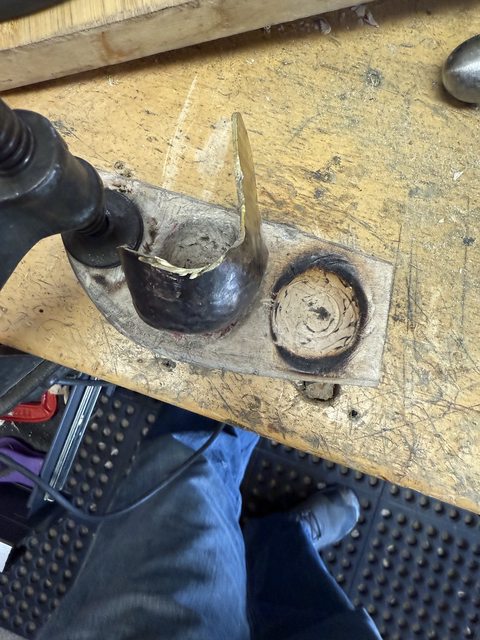
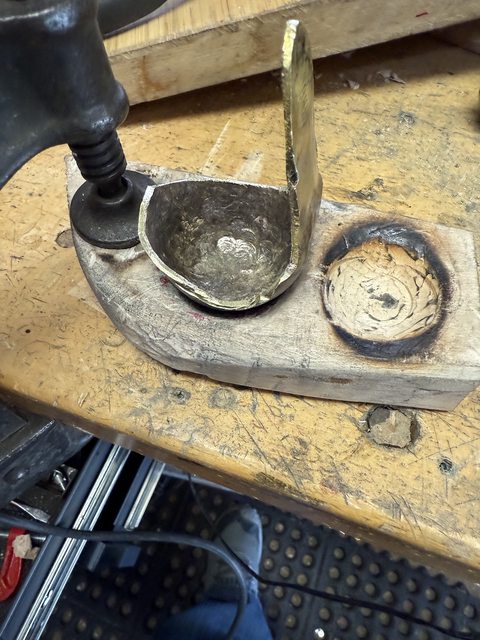
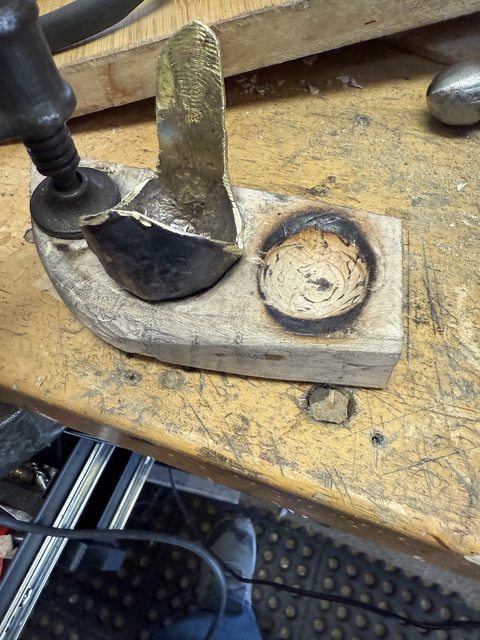