Maybe these pics will give you a better idea.
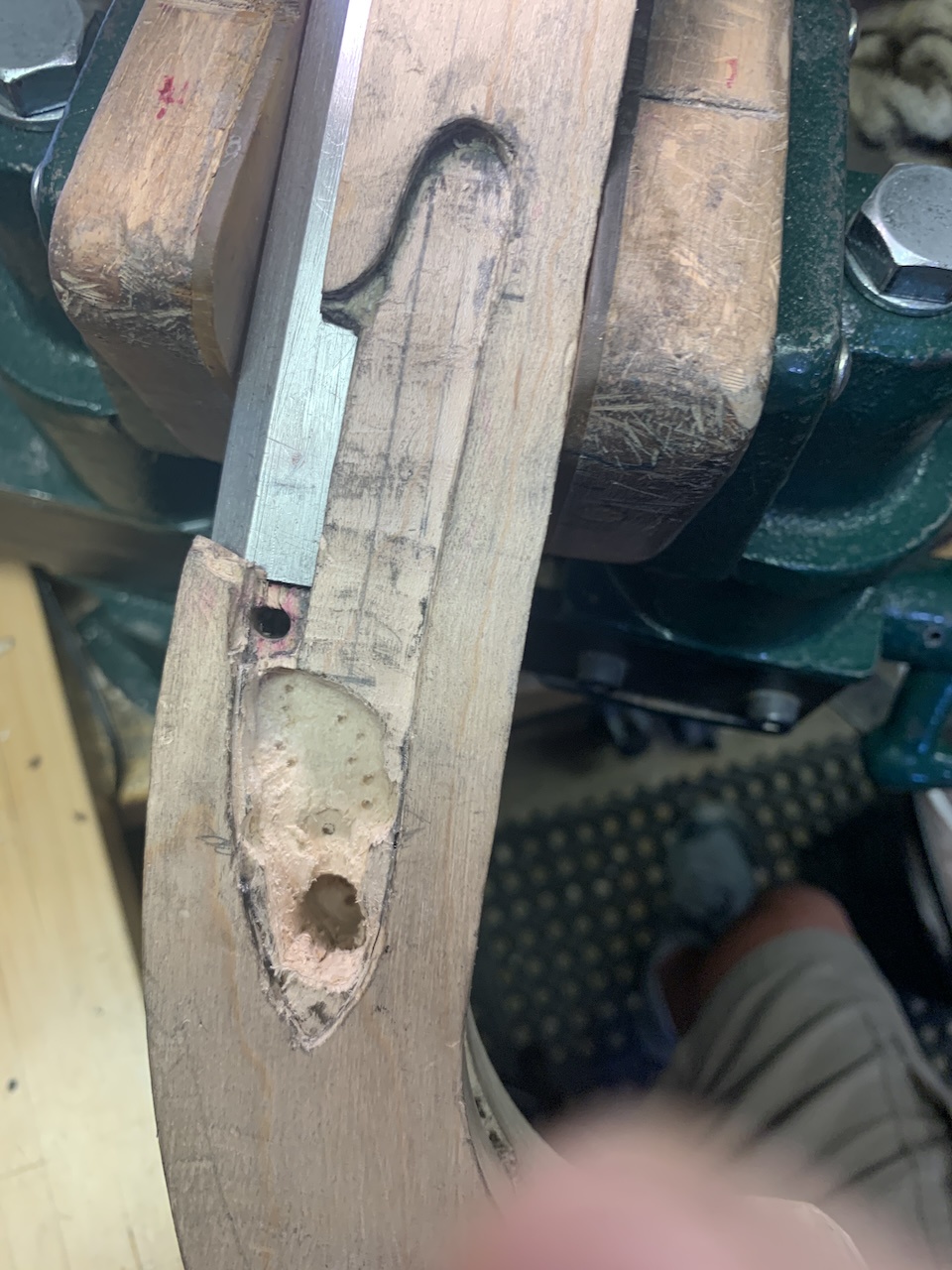
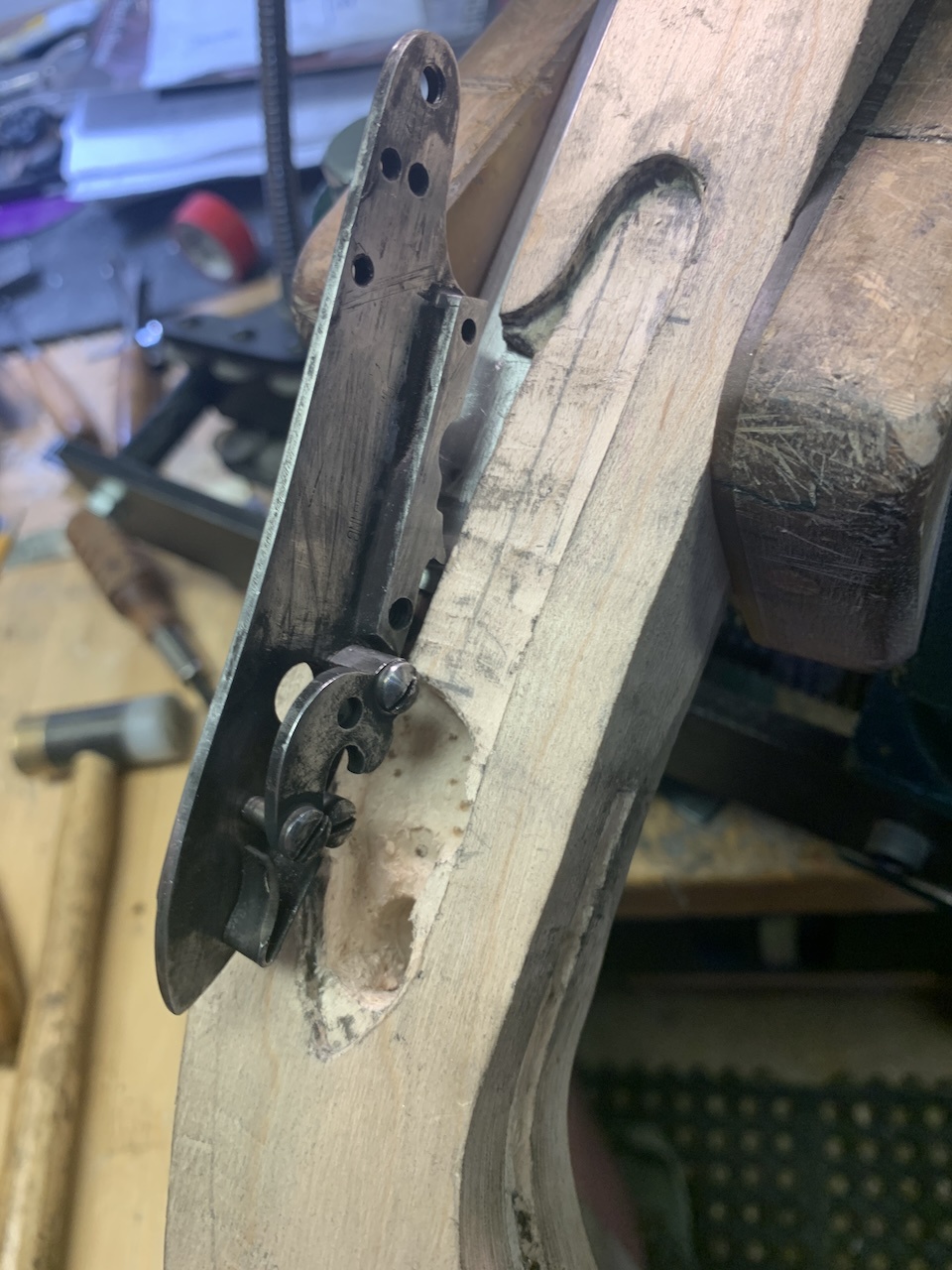
I’m no expert at building, and hope you don’t mistake my comments as criticism. It just appears to me that there is a lot of wood below the lock mortise. I was thinking that you would be removing a whole bunch there but see you already have your trigger plate inlet. I could be way wrong but I am thinking that this pistol will be really chunky.Maybe these pics will give you a better idea.
![]()
![]()
Well....I have the measurements of 1/8"....and I even had 'em marked on the stock. But I squared up the stock a bit more before inletting the TP.....and then I forgot to take off more wood.I’m no expert at building, and hope you don’t mistake my comments as criticism. It just appears to me that there is a lot of wood below the lock mortise. I was thinking that you would be removing a whole bunch there but see you already have your trigger plate inlet. I could be way wrong but I am thinking that this pistol will be really chunky.
Thanks for your input on my providing such a bad example of Early American historical pistol building. Halback and Son had built a few hundred pistols in their/his shop. Another member here has a brace of almost identical ones.Pathfinder,
That is a perfect example of what NOT to do. Obviously, not all the builders of old were great craftsmen. Looks like he was “making do” with parts that weren’t the best choices.
Look at Manton, or Nock, you’ll never see anything like that.
Sorry, off the soap box now.
Thank you for your very kind words. I haven't built a lot, only 3 rifles and one pistol.....and hours and hours of reading build books and on line research. I'm still very much an amateur.Methinks you have building experience a'plenty. I'm impressed. Will the finished product be for you, for sale, for a gift?
You're a true Craftsman!Today I decided to make my Trigger Plate (TP) for the pistol. I cut some metal, cut the trigger slot, then silver soldered two lugs that will be the trigger pivot point. I left the lugs high so I could fit it once the lock and TP are inletted.
![]()
![]()
![]()
![]()
Your comment is very kind. But honestly, I'm just an amateur at best.You're a true Craftsman!