- Joined
- Nov 26, 2005
- Messages
- 5,247
- Reaction score
- 11,028
Hi,
I shaped the fore stock to almost final form. More wood will come off but I wanted to cut in the fore stock molding before final shaping because they have a unique shape on early Reading guns that is easier to do before final shaping. Normally, I bring the stock to its final shape before cutting any moldings. On most long rifles, I bring the stock almost to final finish, then scribe a line along the ramrod channel using a marking gauge that was my great grandfathers and probably made in the 1870s. I then use a long checkering saw to cut down that line. I do this freehand and do not need any guide, jig, or straight edge. Then I use a dog-leg flat chisel to remove background on the upper side of the line to create a raised edge for the molding. After that I might just smooth the cuts or cut a cove shape into the molding, or add parallel lines. Whatever, the style requires. Reading guns require a bit more wood removal so I do them before final shaping.
I start with a scribed line, then use the checkering saw to cut it. Next, I use the dog-leg chisel to cut away background but I cut more deeply than on other moldings and I tip the chisel such that the side catches in the line and I am almost cutting the wood perpendicular to the edge of the molding. I freshen the line using the checkering saw again, and then cut the back ground away with the dog-leg chisel as before. I smooth out the back ground with a bottoming file that is tilted like the dog leg so the side edge of the file catches in the line, using it as a guide.
Next I use a scraper knife I created from a #6 chip carving knife from WoodCraft. I catch the tip of the skew edge in the line and scrape the raised edge of the molding. I round that edge over slightly so that the molding line becomes more of a "V" channel and the molding bulges out a little from the edge and then is rounded over (or flattened on some guns) to the ramrod groove.
The step at the rear ramrod pipe also is a bit different. It bulges a little about the step with the bulge usually merging into the simple carving around the rear pipe tang.
I will leave cleaning up and finishing the molding until later after I carve around the rear ramrod pipe. Early Reading rifles are deceivingly simple looking but they have many sophisticated details and you have to look closely to see them. I love these rifles for just that reason. Mitch Yates is my "go to" guy when I need help with building early Reading rifles. He is very knowledgeable and made several excellent Reading inspired guns. There is so much interest in building early Lancaster and Christians Spring guns but much less in these wonderful Reading and Berks County rifles. It is ironic because the gun shop at Christians Spring was a tiny affair and it has much more influence on us today simply because the Moravians kept very good records of its operation. Gun making in Reading was almost as large a trade as it was in Lancaster, yet we know so little about it because of few early records. With Jim Kibler's new colonial rifle kit, which looks very much like the work of Andreas Albrecht, another CS and Lancaster maker, I suspect those two places will have even more representation among re-enactors and Reading will be further neglected. This despite the fact that we know Dan Morgan purchased rifles in Reading during the Rev War.
Next up, the wrist and lock area.
dave
I shaped the fore stock to almost final form. More wood will come off but I wanted to cut in the fore stock molding before final shaping because they have a unique shape on early Reading guns that is easier to do before final shaping. Normally, I bring the stock to its final shape before cutting any moldings. On most long rifles, I bring the stock almost to final finish, then scribe a line along the ramrod channel using a marking gauge that was my great grandfathers and probably made in the 1870s. I then use a long checkering saw to cut down that line. I do this freehand and do not need any guide, jig, or straight edge. Then I use a dog-leg flat chisel to remove background on the upper side of the line to create a raised edge for the molding. After that I might just smooth the cuts or cut a cove shape into the molding, or add parallel lines. Whatever, the style requires. Reading guns require a bit more wood removal so I do them before final shaping.
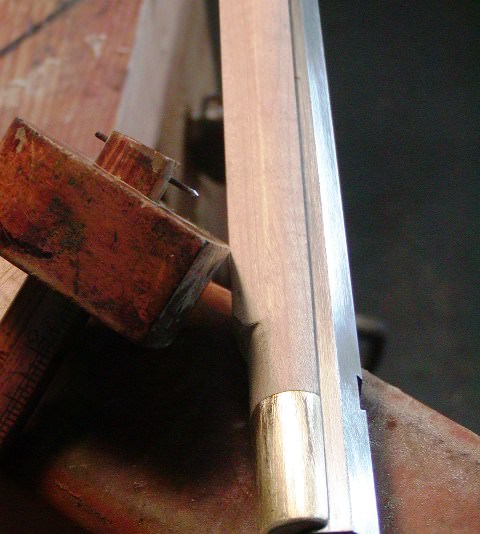
I start with a scribed line, then use the checkering saw to cut it. Next, I use the dog-leg chisel to cut away background but I cut more deeply than on other moldings and I tip the chisel such that the side catches in the line and I am almost cutting the wood perpendicular to the edge of the molding. I freshen the line using the checkering saw again, and then cut the back ground away with the dog-leg chisel as before. I smooth out the back ground with a bottoming file that is tilted like the dog leg so the side edge of the file catches in the line, using it as a guide.
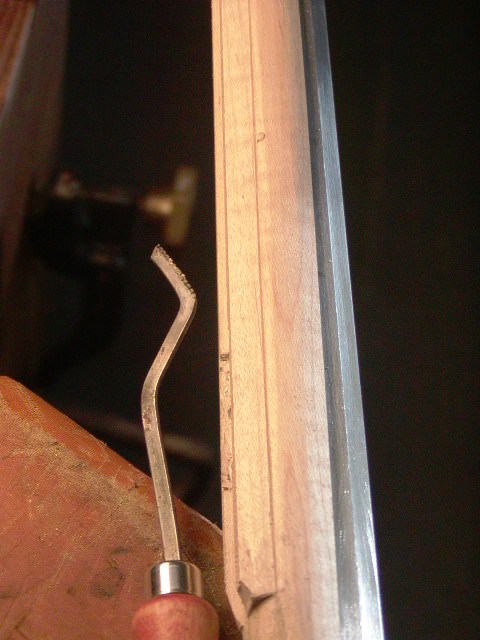
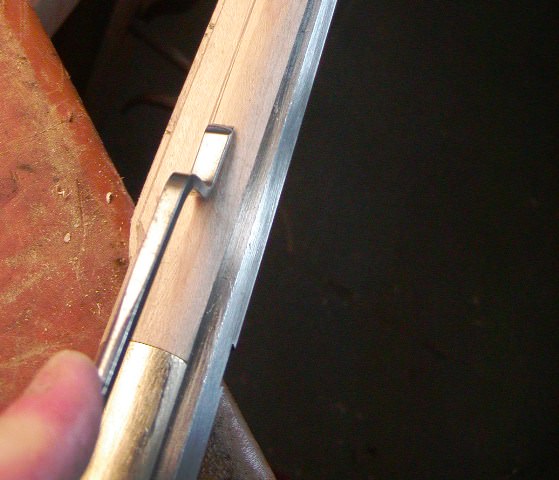
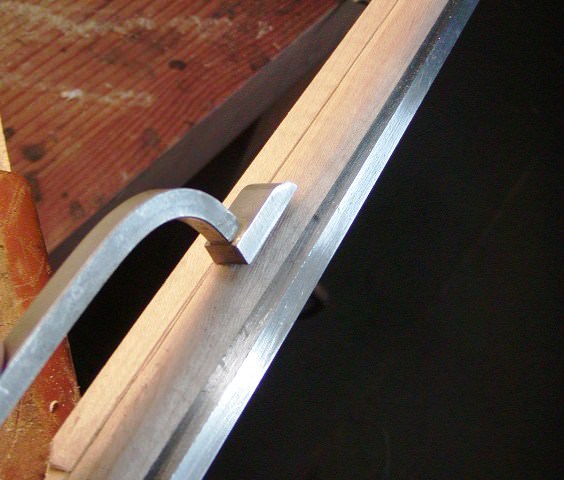
Next I use a scraper knife I created from a #6 chip carving knife from WoodCraft. I catch the tip of the skew edge in the line and scrape the raised edge of the molding. I round that edge over slightly so that the molding line becomes more of a "V" channel and the molding bulges out a little from the edge and then is rounded over (or flattened on some guns) to the ramrod groove.
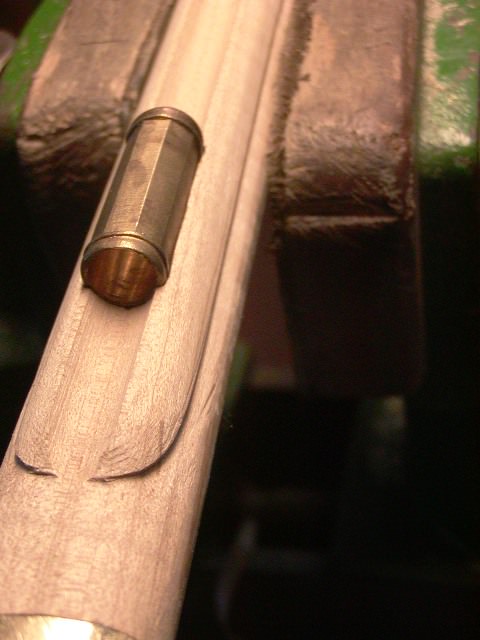
The step at the rear ramrod pipe also is a bit different. It bulges a little about the step with the bulge usually merging into the simple carving around the rear pipe tang.
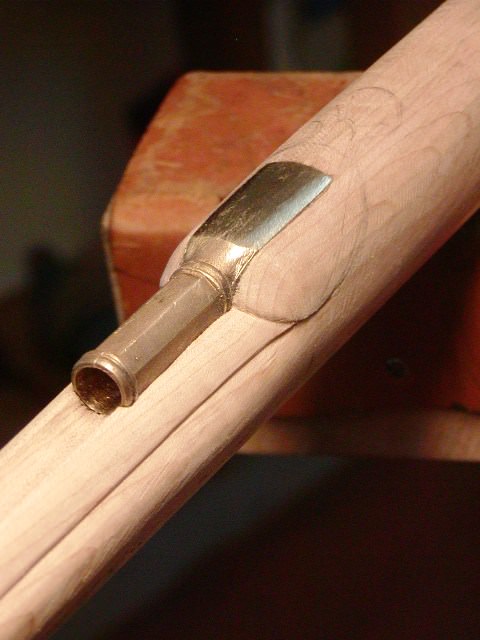
I will leave cleaning up and finishing the molding until later after I carve around the rear ramrod pipe. Early Reading rifles are deceivingly simple looking but they have many sophisticated details and you have to look closely to see them. I love these rifles for just that reason. Mitch Yates is my "go to" guy when I need help with building early Reading rifles. He is very knowledgeable and made several excellent Reading inspired guns. There is so much interest in building early Lancaster and Christians Spring guns but much less in these wonderful Reading and Berks County rifles. It is ironic because the gun shop at Christians Spring was a tiny affair and it has much more influence on us today simply because the Moravians kept very good records of its operation. Gun making in Reading was almost as large a trade as it was in Lancaster, yet we know so little about it because of few early records. With Jim Kibler's new colonial rifle kit, which looks very much like the work of Andreas Albrecht, another CS and Lancaster maker, I suspect those two places will have even more representation among re-enactors and Reading will be further neglected. This despite the fact that we know Dan Morgan purchased rifles in Reading during the Rev War.
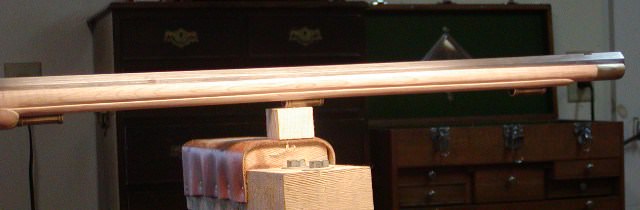
Next up, the wrist and lock area.
dave