Or...just prepping for the days of January\February 2025 when the weather is lousy. I started out with a block of Maple. Sawed the rough shape of the pistol I have a 13" .45 Cal barrel that will be used. Going to pattern it after the Chambers American Flintlock Pistol.
I got the barrel channel cut. Not the tang yet as I need to buy the breech plug, drill and tap the barrel and seat it. Today I received my 12" 5/16" drill bit and finished the ramrod hole. Next is to rough cut the width. Then inlet the tang.....and move on from there!!!
I got the barrel channel cut. Not the tang yet as I need to buy the breech plug, drill and tap the barrel and seat it. Today I received my 12" 5/16" drill bit and finished the ramrod hole. Next is to rough cut the width. Then inlet the tang.....and move on from there!!!
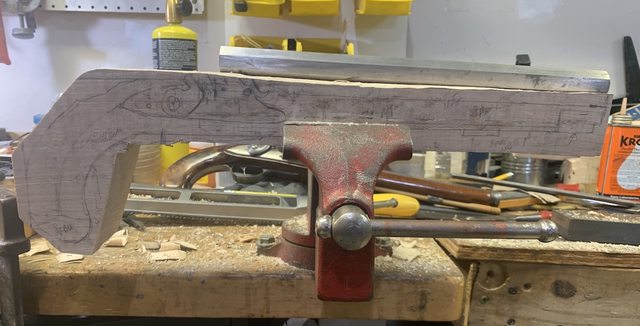
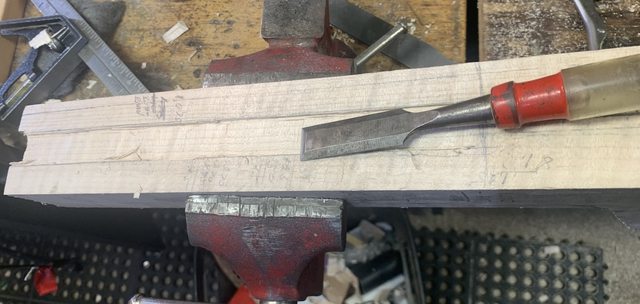

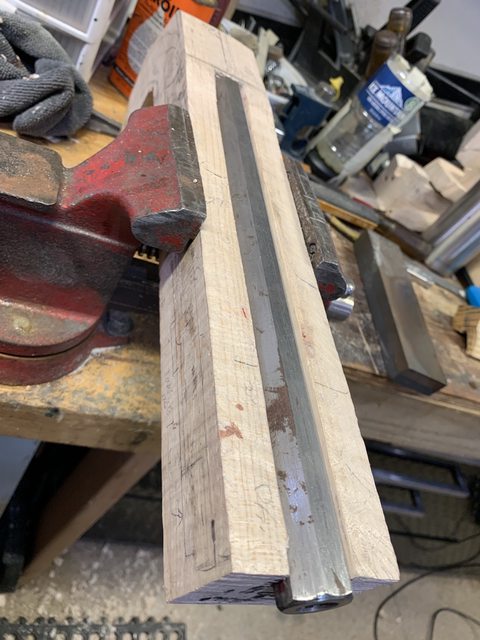
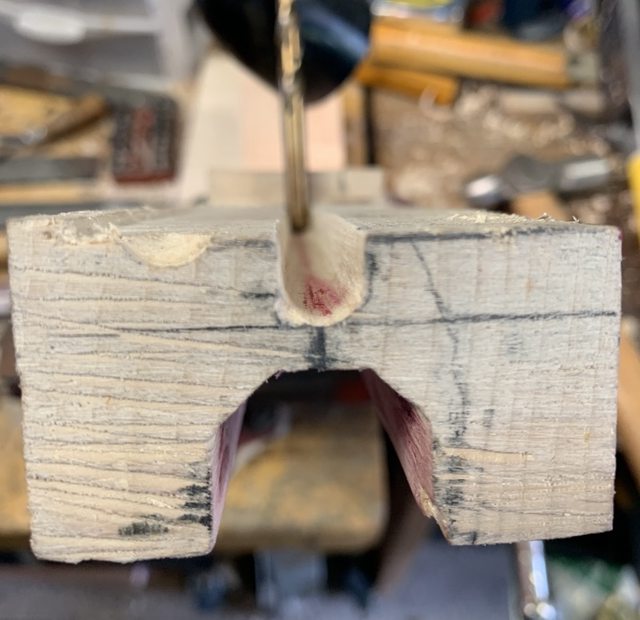
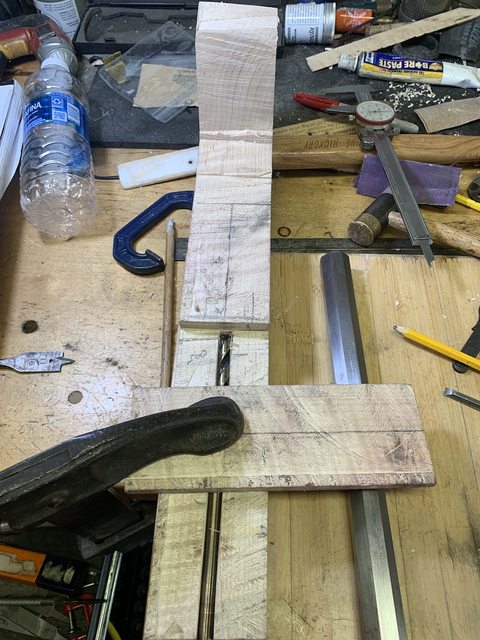
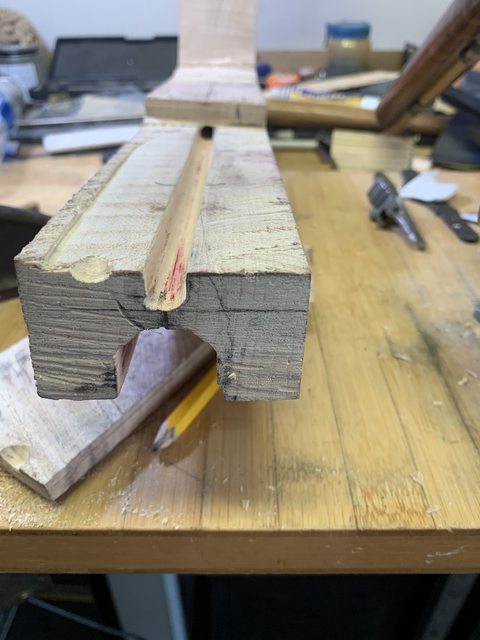